Method and equipment for improving glass quality
A glass, quality technology, used in/or other glass substrates, clarification and homogenization, the production of glass substrates, can solve the problems of uneven temperature of glass liquid, high temperature of molten glass, stripes and other problems
- Summary
- Abstract
- Description
- Claims
- Application Information
AI Technical Summary
Problems solved by technology
Method used
Image
Examples
Embodiment 2
[0075] As shown in Figure 2, this example is 2 parallel clarification zones. Under the condition that the glass flow rate is 10 tons / day, the clarification zone is designed as a cylindrical shape. According to certain experiences and theories, the diameter, wall thickness and length of the clarification zone are determined as shown in the corresponding row of Example 2 in Table 1. Compared with Comparative Example 1, the amount of precious metal used in Example 2 is 20.48 kg less; the glass temperature difference is reduced from ±3°C to ±1°C; the number of bubbles larger than 0.1mm per kilogram of glass plate does not exceed 0.5; the clarification zone The operating temperature can drop from 1680°C to 1650°C; the life of the clarification zone is extended from 21 months to 26 months.
Embodiment 3
[0077] As shown in Figure 3, this example is three parallel clarification zones. Under the condition that the glass flow rate is 10 tons / day, the clarification zone is designed as a cylindrical shape. According to certain experiences and theories, the diameter, wall thickness and length of the clarification zone are determined as shown in the row corresponding to Example 3 in Table 1. Compared with Comparative Example 1, the amount of precious metal used in Example 3 is 36.65 kg less; the glass temperature difference is reduced from ±3°C to ±0.7°C; the number of bubbles larger than 0.1mm per kilogram of glass plate does not exceed 0.2; the clarification zone The operating temperature dropped from 1680°C to 1620°C, and the lifetime of the clarification channel was extended from 21 months to 26.5 months.
[0078] Through the above examples, it can be clearly seen that when the flow rate of glass is 10 tons / day, the two embodiments of the parallel clarification zone are more eff...
Embodiment 5
[0082] As shown in Figure 2, this example is 2 parallel clarification zones. Under the condition that the glass flow rate is 12 tons / day, the clarification zone is designed as a cylindrical shape. According to certain experiences and theories, the diameter, wall thickness and length of the clarification zone are determined as shown in the corresponding row of Example 5 in Table 1. Compared with Comparative Example 4, the amount of precious metal used in Example 5 is 35.68 kg less; the glass temperature difference is reduced from ±3.3°C to ±1.5°C; the number of bubbles larger than 0.1mm per kilogram of glass plate does not exceed 0.6; the clarification zone The operating temperature can drop from 1680°C to 1650°C; the life of the clarification zone is extended from 19 months to 24.5 months.
PUM
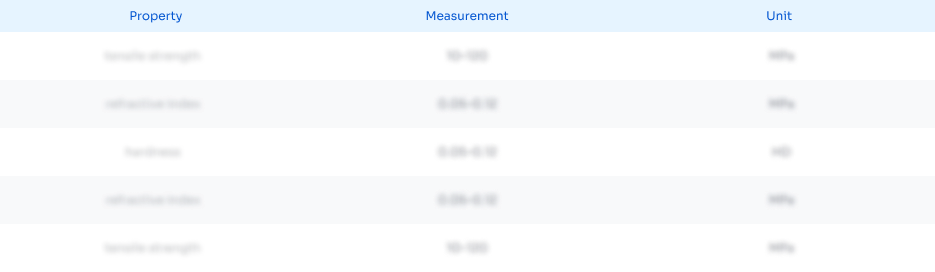
Abstract
Description
Claims
Application Information

- Generate Ideas
- Intellectual Property
- Life Sciences
- Materials
- Tech Scout
- Unparalleled Data Quality
- Higher Quality Content
- 60% Fewer Hallucinations
Browse by: Latest US Patents, China's latest patents, Technical Efficacy Thesaurus, Application Domain, Technology Topic, Popular Technical Reports.
© 2025 PatSnap. All rights reserved.Legal|Privacy policy|Modern Slavery Act Transparency Statement|Sitemap|About US| Contact US: help@patsnap.com