Process for preparing fluorin, silicon, epoxide modified low surface energy acrylate emulsion for heavy anti-corrosion paint
A fluorinated acrylate, high-quality epoxy technology, used in anti-corrosion coatings, etc., can solve problems such as affecting the use value, poor mechanical strength, poor water resistance, etc., achieve excellent elasticity and crack resistance, improve stain resistance, reduce cost effect
- Summary
- Abstract
- Description
- Claims
- Application Information
AI Technical Summary
Problems solved by technology
Method used
Examples
Embodiment 1
[0041] The main monomer is a composite main monomer composed of 25-30 g of n-butyl acrylate, 5-10 g of methyl methacrylate and 5-10 g of styrene.
[0042] ① Add 0.5% to 1% nonionic emulsifier allyloxy nonylphenol polyoxyethylene ether and 0.5% to 1.5% anionic emulsifier to a 250ml four-necked flask equipped with an electric stirrer, condenser and thermometer Sodium hydrocarbyl acrylate-2-ethanesulfonate and 30g of water, the temperature of the water bath reaches 82±2°C, and 0.1% to 0.4% of the initiator ammonium persulfate is added;
[0043]② After 10 to 30 minutes, the main monomer is composed of 25 to 30 g of n-butyl acrylate, 5 to 10 g of methyl methacrylate and 5 to 10 g of styrene, and 3% to 15% of epoxy monomer methyl Glycidyl acrylate, the remaining nonionic emulsifier and anionic emulsifier, half of the pre-emulsion composed of 0.05% to 0.15% initiator and 25g water are added dropwise to the reaction bottle within 1h to 1.5h, and the remaining 1.0% to 3.0% of the noni...
Embodiment 2
[0047] The main monomer is a composite monomer composed of 25-30 g of n-butyl acrylate and 10-20 g of styrene.
[0048] ① Add 0.5% to 1% nonionic emulsifier polyoxyethylene arylphenol acrylate, 0.5% to 1.5% anionic emulsifier hydrocarbyl acrylic acid- 2-Sodium ethanesulfonate and 30g of water are heated up to a water bath temperature of 82±2°C, and 0.1% to 0.4% of initiator potassium persulfate is added;
[0049] ② After 10-30 minutes, the main monomer n-butyl acrylate 25-30g and styrene 10-20g composite monomer, 3%-15% epoxy monomer glycidyl methacrylate, and the remaining non-ionic emulsification half of the pre-emulsion composed of 0.05% to 0.15% initiator and 25g water is added dropwise to the reaction bottle within 1h to 1.5h, and the remaining nonionic emulsifier is 1.0% to 3.0% , the remaining anionic emulsifier 2.0% to 4.5%;
[0050] ③Add all the fluorine monomer nonadecafluoroheptyl acrylate, silicon monomer vinyltriethoxysilane and remaining epoxy monomer glycidyl ...
Embodiment 3
[0053] The main monomer is a composite monomer composed of 25-30g of n-butyl acrylate and 10-20g of methyl methacrylate.
[0054] ① Add 0.5% to 1% nonionic emulsifier polyoxyethylene arylphenol acrylate, 0.5% to 1.5% anionic emulsifier p-styrene Sodium sulfonate and 30g of water are heated up to a water bath temperature of 82±2°C, and 0.1% to 0.4% of initiator potassium persulfate is added;
[0055] ② After 10-30 minutes, mix the main monomer n-butyl acrylate 25-30g, methyl methacrylate 10-20g composite monomer, 3%-15% epoxy monomer glycidyl methacrylate, and the remaining Nonionic emulsifier and anionic emulsifier, half of the pre-emulsion composed of 0.05% ~ 0.15% initiator and 25g water are added dropwise into the reaction bottle within 1h ~ 1.5h, and the remaining nonionic emulsifier is 1.0% ~3.0%, the remaining anionic emulsifier 2.0%~4.5%;
[0056] ③ Add all the fluorine monomer dodecafluoroheptyl methacrylate, the silicon monomer γ-methacryloxypropyl trimethoxysilane ...
PUM
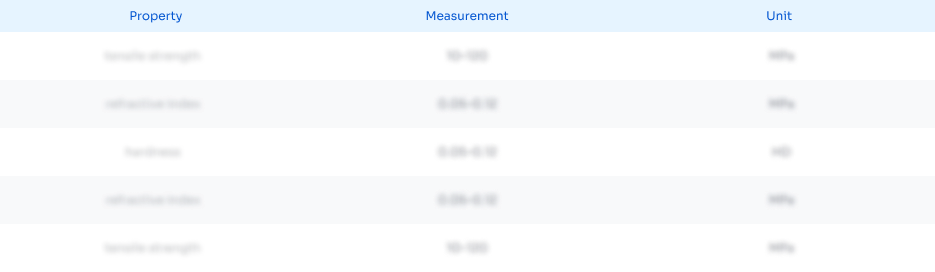
Abstract
Description
Claims
Application Information

- R&D
- Intellectual Property
- Life Sciences
- Materials
- Tech Scout
- Unparalleled Data Quality
- Higher Quality Content
- 60% Fewer Hallucinations
Browse by: Latest US Patents, China's latest patents, Technical Efficacy Thesaurus, Application Domain, Technology Topic, Popular Technical Reports.
© 2025 PatSnap. All rights reserved.Legal|Privacy policy|Modern Slavery Act Transparency Statement|Sitemap|About US| Contact US: help@patsnap.com