Ball end mill
A ball-end mill and ball-end technology, used in milling cutters, cutters for milling machines, forming cutters, etc., can solve the problems of inability to cut, large cutting resistance, high-speed cutting, etc., to achieve processing efficiency and prevent sharpness. The effect of reducing the speed and improving the processing efficiency
- Summary
- Abstract
- Description
- Claims
- Application Information
AI Technical Summary
Problems solved by technology
Method used
Image
Examples
Embodiment Construction
[0037] Hereinafter, preferred embodiments of the present invention will be described with reference to the accompanying drawings. Fig. 1 is a front view of a multi-flute ball end mill (hereinafter simply referred to as a ball end mill) 1 as an embodiment of the present invention, and Fig. 2 is a tip side of the ball end mill 1 (right side in Fig. 1 ). side), FIG. 3 is a side view of the ball end mill 1 viewed from the direction of arrow II in FIG. 1 . First, the overall structure of the ball end mill 1 will be described with reference to these FIGS. 1 to 3 .
[0038] The ball end mill 1 mainly includes: a tool body 2 having an axis L, and a cutting edge 3 coaxially connected to the end side of the tool body 2, and is used for free-form surface machining or Finishing of chamfering, etc. This ball end mill 1 is mounted on a processing machine such as a machining center via a holder (not shown) holding the shank portion 2a of the tool body 2, and is driven to rotate around the ...
PUM
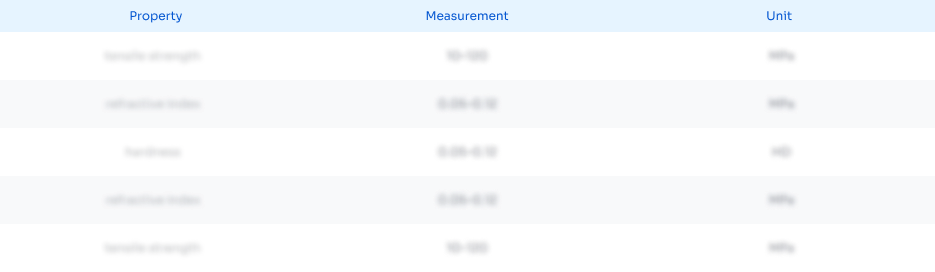
Abstract
Description
Claims
Application Information

- R&D
- Intellectual Property
- Life Sciences
- Materials
- Tech Scout
- Unparalleled Data Quality
- Higher Quality Content
- 60% Fewer Hallucinations
Browse by: Latest US Patents, China's latest patents, Technical Efficacy Thesaurus, Application Domain, Technology Topic, Popular Technical Reports.
© 2025 PatSnap. All rights reserved.Legal|Privacy policy|Modern Slavery Act Transparency Statement|Sitemap|About US| Contact US: help@patsnap.com