Generator magnetic pole precision forging method
A generator and magnetic pole technology, applied in the direction of metal processing equipment, etc., can solve problems such as difficulty in meeting performance and quality requirements, lower electromagnetic performance of magnetic poles, long manufacturing process, etc., to improve plastic flow conditions, improve forming accuracy and product qualification rate, The effect of improving productivity
- Summary
- Abstract
- Description
- Claims
- Application Information
AI Technical Summary
Problems solved by technology
Method used
Image
Examples
Embodiment Construction
[0019] The present invention will be further described below in conjunction with FIGS. 1-9 .
[0020] The method for precision forging forming of generator magnetic poles is realized according to the following steps:
[0021] 1) Raw material blanking: Cut the raw material (bar) into segments, according to the formula D b =D p -C determines the diameter of the material section, where the diameter of the magnetic pole boss is D p , the material section diameter is D b , C=0~20 mm, the size of the axial height H of the material section is determined by the condition that the blank volume and the magnetic pole volume are equal; as shown in Figure 1, Figure 2, Figure 3, and Figure 5, the diameter of the boss is determined by the p Φ52 mm, determine the material section diameter D b It is Φ45 mm, where C is 7 mm; the volume of the forging is calculated according to the forging diagram, and the height of the discharge section is calculated to be 111 mm according to the principle ...
PUM
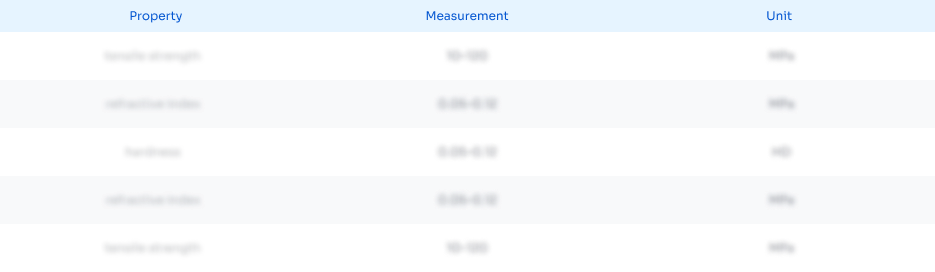
Abstract
Description
Claims
Application Information

- R&D
- Intellectual Property
- Life Sciences
- Materials
- Tech Scout
- Unparalleled Data Quality
- Higher Quality Content
- 60% Fewer Hallucinations
Browse by: Latest US Patents, China's latest patents, Technical Efficacy Thesaurus, Application Domain, Technology Topic, Popular Technical Reports.
© 2025 PatSnap. All rights reserved.Legal|Privacy policy|Modern Slavery Act Transparency Statement|Sitemap|About US| Contact US: help@patsnap.com