Laser measuring method for non-contact type micro-rotor vibration displacement
A technology of rotor vibration and laser measurement, which is applied in the field of micro-electromechanical systems, achieves the effects of simple implementation, high measurement accuracy, and avoiding low accuracy
- Summary
- Abstract
- Description
- Claims
- Application Information
AI Technical Summary
Problems solved by technology
Method used
Image
Examples
Embodiment 1
[0020] Select a 6mm electromagnetic thin-film micro-motor, its main technical parameters are: the diameter of the micro-rotor disk is D=6mm, the thickness of the disk is t=1.2mm, the shaft length is L=3mm, the shaft diameter is d=1.5mm, the working voltage 10V ~ 13V. The sampling frequency is 60Hz.
[0021] In this embodiment, in order to achieve speed control and improve positioning accuracy, a constant current subdivision drive circuit system is used to control the excitation current in the stator winding of the micro-motor, and to synthesize a magnetic field vector with constant amplitude and uniform angle change, so that the micro-motor runs smoothly ; Using CCD scanning imaging technology to sample and analyze the vibration process of the micro-rotor under the condition of controllable speed, the displacement sensor in the CCD scanning system obtains the image signal of the micro-rotor, stores it in the buffer of the signal acquisition card, and then controls it by the an...
Embodiment 2
[0024] Select a 2mm electromagnetic thin-film micro-motor, its main technical parameters are: the overall size is 2.3mm×2.3mm×1.5mm, the diameter of the micro-rotor is D=2mm, the working voltage is 8V, the working current is 70mA, and the maximum no-load speed is 25000rpm , the weight is 38mg, the speed range is 50:1, the maximum output torque is 2.8μN·m, and the rotor system adopts double-stator-single-rotor sandwich structure. The sampling frequency is 60Hz.
[0025]In this embodiment, in order to control the speed of the micro-rotor and improve the positioning accuracy, a constant current subdivision drive circuit system is used to control the excitation current in the stator winding of the micro-motor, and to synthesize a magnetic field vector with constant amplitude and uniform angle change, so that the micro-motor The operation is stable; CCD scanning imaging technology is used to sample and analyze the vibration process of the micro-rotor under the condition of controll...
PUM
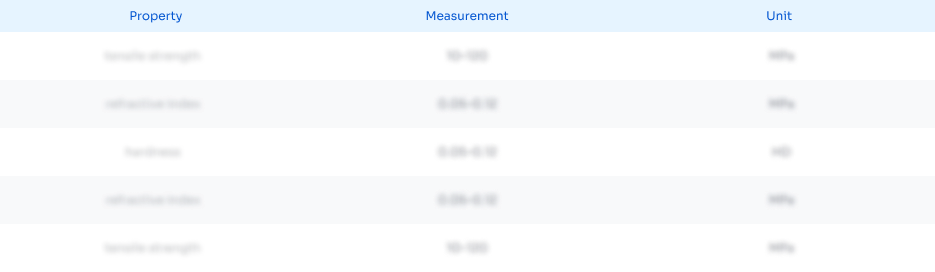
Abstract
Description
Claims
Application Information

- Generate Ideas
- Intellectual Property
- Life Sciences
- Materials
- Tech Scout
- Unparalleled Data Quality
- Higher Quality Content
- 60% Fewer Hallucinations
Browse by: Latest US Patents, China's latest patents, Technical Efficacy Thesaurus, Application Domain, Technology Topic, Popular Technical Reports.
© 2025 PatSnap. All rights reserved.Legal|Privacy policy|Modern Slavery Act Transparency Statement|Sitemap|About US| Contact US: help@patsnap.com