Elevator control system
An elevator control device and motor control technology, applied in the field of elevator control devices, can solve problems such as increased heat generation of motors and inverters, equipment failure, motor and inverter failures, etc.
- Summary
- Abstract
- Description
- Claims
- Application Information
AI Technical Summary
Problems solved by technology
Method used
Image
Examples
Embodiment approach 1
[0020] figure 1 It is a block diagram showing the elevator apparatus according to Embodiment 1 of the present invention. In the figure, a driving device (tractor) 1 is provided on the upper part of the hoistway. The traction machine 1 has a motor unit 2 and a traction sheave 3 rotated by the motor unit 2 . A braking device (not shown) for braking the rotation of the traction sheave 3 is provided in the motor unit 2 .
[0021] And, a free-rotating guide wheel 4 is provided on the top of the hoistway. A plurality of master ropes 5 (only one is shown in the figure) are wound around the traction sheave 3 and the guide sheave 4 . At one end of the main rope 5, a car 6 is suspended. A counterweight 7 is provided at the other end of the main rope 5 .
[0022] The weight of the counterweight 7 is set to be balanced when the carrying weight of the car 6 is approximately half load of the maximum carrying weight (full load).
[0023] The operation of the motor unit 2 is driven by p...
Embodiment approach 2
[0041] then, Figure 6It is a block diagram showing the elevator apparatus according to Embodiment 2 of the present invention. In the figure, the temperatures of the motor unit 2 and the inverter 8 are detected by the temperature detection unit 17 . The abnormality detection part 11 is provided with the abnormality judgment part 18 which judges the abnormal state of an elevator. The abnormality determination unit 18 determines an abnormal state based on signals from the car load detection unit 9 , the speed control unit 13 , and the temperature detection unit 17 , and sends information about the abnormality to the speed pattern generation unit 12 and the speed control unit 13 . Other configurations are the same as those in Embodiment 1.
[0042] Figure 7 yes means Figure 6 An explanatory diagram of a first example of the abnormality judgment method implemented by the abnormality judgment unit 18 of . The abnormality judging part 18, for example, calculates the differenc...
PUM
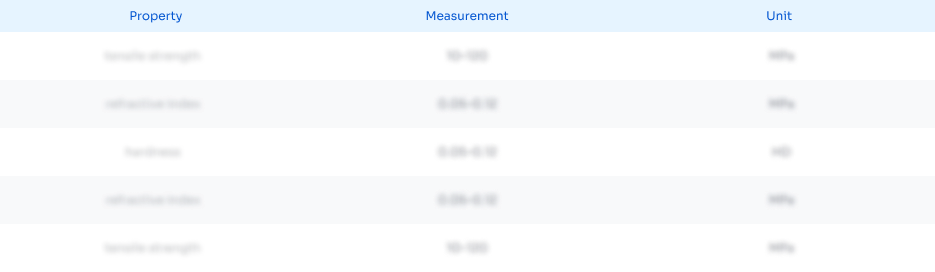
Abstract
Description
Claims
Application Information

- R&D Engineer
- R&D Manager
- IP Professional
- Industry Leading Data Capabilities
- Powerful AI technology
- Patent DNA Extraction
Browse by: Latest US Patents, China's latest patents, Technical Efficacy Thesaurus, Application Domain, Technology Topic, Popular Technical Reports.
© 2024 PatSnap. All rights reserved.Legal|Privacy policy|Modern Slavery Act Transparency Statement|Sitemap|About US| Contact US: help@patsnap.com