Method of producing fuel oil by coal tar hydrogenation modifying
A hydrogenation reforming and coal tar technology, which is applied in the fields of hydrogenation treatment process, petroleum industry, gasoline stabilization, etc., can solve the problems of unguaranteed long-term operation, unresolved strong exothermic effect, high asphaltenes and benzene insolubles, and achieves The effect of improving product quality, reducing olefin and aromatic content, and reducing total temperature rise
- Summary
- Abstract
- Description
- Claims
- Application Information
AI Technical Summary
Problems solved by technology
Method used
Examples
Embodiment 1
[0021]The raw material oil is a mixture of catalytic diesel oil and medium and low temperature full-distilled coal tar I in a weight ratio of 1:10. The properties are shown in Table 1. The first hydrogenation reactor is filled with HG-1 hydrogenation protection agent from top to bottom, the self-made pre-hydrogenation catalyst, and the second hydrogenation reactor is filled with the self-made main hydrogenation catalyst, the filling volume of the three catalysts The ratio is 2:3:10, and the hydrogenation reaction conditions and test results are shown in Table 2 and Table 3. The products were cut into light oil fraction (≤205°C), diesel fraction (205°C to 325°C), and heavy oil fraction (>325°C). The composition of gasoline, diesel, and heavy oil after cutting is shown in Table 4.
[0022] Item
[0023] Test number
[0024] Test number
[0025] Test number
Embodiment 2
[0027] The raw material oil is a mixture of hydrogenated diesel oil and medium and low temperature full-cut coal tar II in a weight ratio of 1:1 and 10:1 respectively. The properties are shown in Table 5. The first hydrogenation reactor is filled with HG-1 hydrogenation protection agent from top to bottom, the self-made pre-hydrogenation catalyst, and the second hydrogenation reactor is filled with the self-made main hydrogenation catalyst, the filling volume of the three catalysts The ratio is 3:3:10, and the hydrogenation reaction conditions and test results are shown in Table 6 and Table 7. The products were cut into gasoline fraction (≤205°C), diesel fraction (205°C~325°C), and heavy oil fraction (>325°C). The composition and properties of gasoline, diesel, and heavy oil after cutting are shown in Table 8, Table 9, and Table 10. And table 11.
[0028] Item
[0029] Test number
[0030] Test number
[0031]
[0032] Test nu...
Embodiment 3
[0036] The feedstock oil is a mixture of hydrogenated diesel oil and high-temperature full-distillate coal tar III in a weight ratio of 1:1. The first hydrogenation reactor is filled with HG-1 hydrogenation protection agent from top to bottom, the self-made pre-hydrogenation catalyst, and the second hydrogenation reactor is filled with the self-made main hydrogenation catalyst, the filling volume of the three catalysts The ratio is 3:3:10, and the hydrogenation reaction conditions and test results are shown in Table 12 and Table 13.
[0037] Test number
[0038] Item
PUM
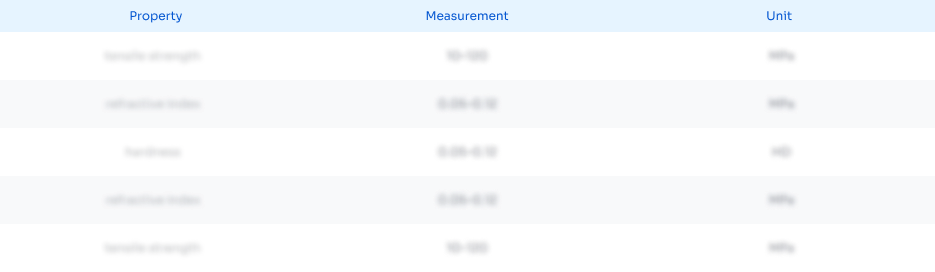
Abstract
Description
Claims
Application Information

- R&D
- Intellectual Property
- Life Sciences
- Materials
- Tech Scout
- Unparalleled Data Quality
- Higher Quality Content
- 60% Fewer Hallucinations
Browse by: Latest US Patents, China's latest patents, Technical Efficacy Thesaurus, Application Domain, Technology Topic, Popular Technical Reports.
© 2025 PatSnap. All rights reserved.Legal|Privacy policy|Modern Slavery Act Transparency Statement|Sitemap|About US| Contact US: help@patsnap.com