High-aluminium vanadine moulding sand, and its preparing method
A high-alumina vanadium clay and molding sand technology, which is applied in the field of casting molding materials, can solve problems such as difficulty in cutting workpieces, peeling off of sand coating layers, and affecting product quality, and achieve the effects of saving raw materials, smooth surfaces, and improving working conditions
- Summary
- Abstract
- Description
- Claims
- Application Information
AI Technical Summary
Problems solved by technology
Method used
Examples
Embodiment Construction
[0008] The ratio of high alumina bauxite molding sand is (kg) by weight:
[0009] High alumina bauxite 75 High alumina powder 30 85% dilute phosphoric acid solution 10 Bentonite 3.
[0010] Preparation method: Add the quantified high-alumina vanadium clay and high-alumina powder into a sand mill for dry mixing. After mixing well, gradually add 85% dilute phosphoric acid solution for wet mixing, and finally add bentonite. After mixing well, take them all out. Reserve, use up the mixed molding sand within 12 hours to prevent hardening and scrapping.
PUM
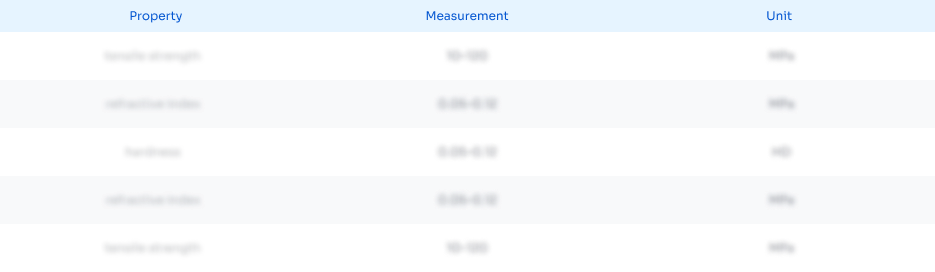
Abstract
Description
Claims
Application Information

- R&D
- Intellectual Property
- Life Sciences
- Materials
- Tech Scout
- Unparalleled Data Quality
- Higher Quality Content
- 60% Fewer Hallucinations
Browse by: Latest US Patents, China's latest patents, Technical Efficacy Thesaurus, Application Domain, Technology Topic, Popular Technical Reports.
© 2025 PatSnap. All rights reserved.Legal|Privacy policy|Modern Slavery Act Transparency Statement|Sitemap|About US| Contact US: help@patsnap.com