Fluorinated hydrogenation catalyst with silicon oxide-alumina as carrier and its production
A technology of silica and alumina, applied in physical/chemical process catalysts, aromatics hydrogenation refining, chemical instruments and methods, etc., can solve the problems of low activity and limited improvement, and achieve the effect of high activity
- Summary
- Abstract
- Description
- Claims
- Application Information
AI Technical Summary
Problems solved by technology
Method used
Image
Examples
example 1
[0027] Take by weighing 2000 grams of aluminum hydroxide powder (dried rubber powder produced by Changling Refining and Chemical Company Catalyst Factory, 70% by weight on a dry basis) and 631 grams of silica sol (Qingdao Ocean Chemical Plant product) containing 25% of silicon dioxide, after mixing Extrude into a butterfly bar with a circumscribed circle diameter of 1.3 mm using an extruder, dry the wet bar at 120° C. for 4 hours, and bake it at 600° C. for 3 hours to obtain carrier S1. The silicon oxide content in the carrier S1 is 10.1% by weight.
[0028]Weigh 200 grams of carrier S1, impregnate the carrier with 176 ml of aqueous solution containing 16.9 grams of ammonium fluoride (analytical grade, product of Beijing Chemical Plant) for 2 hours, dry at 120°C for 3 hours, and roast at 480°C for 3 hours to obtain fluorine-containing Silica-alumina support. With 170 milliliters of the aqueous solution containing ammonium paramolybdate (chemically pure, Beijing Chemical Plant ...
example 2
[0030] Weigh 200 g of carrier S1, impregnate the carrier with 176 ml of an aqueous solution containing 19.1 g of ammonium fluoride for 2 hours, dry at 120° C. for 3 hours, and calcinate at 420° C. for 3 hours to obtain a fluorine-containing silica-alumina carrier. Impregnate the above-mentioned carrier with 170 ml of an aqueous solution containing 24.7 grams of ammonium paramolybdate for 3 hours, dry at 280°C for 8 hours, then impregnate with 160 ml of an aqueous solution containing 24.6 grams of nickel nitrate and 66.7 grams of ammonium metatungstate for 3 hours, and wet the strip at 120 ℃ drying for 4 hours and 500 ℃ calcining for 4 hours to obtain catalyst C2. The composition of catalyst C2 after calcination is listed in Table 1.
example 3
[0032] Weigh 200 g of carrier S1, impregnate the carrier with 176 ml of an aqueous solution containing 8.9 g of ammonium fluoride for 2 hours, dry at 120° C. for 3 hours, and calcinate at 420° C. for 3 hours to obtain a fluorine-containing silica-alumina carrier. Impregnate the above-mentioned carrier with 170 ml of an aqueous solution containing 17.5 grams of ammonium paramolybdate for 3 hours, dry at 280°C for 8 hours, then impregnate with 162 ml of an aqueous solution containing 44.3 grams of nickel nitrate and 74.4 grams of ammonium metatungstate for 3 hours, and wet the strip at 120 ℃ drying for 4 hours, followed by calcination at 500 ℃ for 4 hours to obtain catalyst C3. The composition of catalyst C3 after calcination is listed in Table 1.
PUM
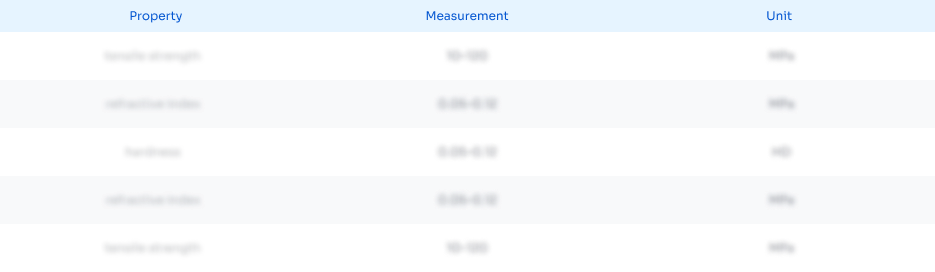
Abstract
Description
Claims
Application Information

- R&D
- Intellectual Property
- Life Sciences
- Materials
- Tech Scout
- Unparalleled Data Quality
- Higher Quality Content
- 60% Fewer Hallucinations
Browse by: Latest US Patents, China's latest patents, Technical Efficacy Thesaurus, Application Domain, Technology Topic, Popular Technical Reports.
© 2025 PatSnap. All rights reserved.Legal|Privacy policy|Modern Slavery Act Transparency Statement|Sitemap|About US| Contact US: help@patsnap.com