Reduction method for copper-radic catalyst for reforming methanol vapour to produce hydrogen
A copper-based catalyst, reforming hydrogen production technology, applied in chemical instruments and methods, metal/metal oxide/metal hydroxide catalysts, physical/chemical process catalysts, etc., can solve the complex process and increase equipment investment. and other problems, to achieve the effect of uniform restoration, easy temperature control and investment saving.
- Summary
- Abstract
- Description
- Claims
- Application Information
AI Technical Summary
Problems solved by technology
Method used
Examples
Embodiment 1
[0019] Add 60ml methanol steam reforming hydrogen production catalyst to the gas phase reactor, the weight percentage of copper oxide in the catalyst is 65%, the vaporization part of the device, the reaction part heats up simultaneously, the temperature rise rate is 20 ℃ / h, simultaneously with the gas space velocity 1000h -1 Air is introduced, and when the temperature rises to 110°C, the air is stopped. Then use a metering pump at an air speed of 1200h -1 Pass into deionized water, and pass through to account for the volume percentage of both to be 0.5% of H 2 (ie 0.37L / h), the heating rate is 10°C / h. Stop feeding H when the temperature rises to 200°C 2 and water, and use a metering pump at the liquid space velocity for 1h -1 Pass in 0.5% methanol aqueous solution, continue to heat up, the temperature rise rate is 10°C / h, stop the temperature rise when the temperature rises to 230°C, continue to use the liquid space velocity for 1h -1 Introduce 1% methanol aqueous solutio...
Embodiment 2
[0024] Add 60ml methanol steam reforming hydrogen production catalyst to the gas phase reactor, the weight percentage of copper oxide in the catalyst is 55%, the vaporization part of the device, the reaction part is heated up at the same time, the temperature rise rate is 20 ℃ / h, and the air space velocity is 1500h at the same time -1 Air is introduced, and when the temperature rises to 120°C, the air is stopped. Then use a metering pump at an air-space velocity of 1500h -1 Pass into deionized water, and pass through to account for the volume percentage of both to be 1% H 2 , the heating rate is 10°C / h. Stop feeding H when the temperature rises to 160°C 2 and water, and use a metering pump at a liquid space velocity of 1.2h -1 Pass in 1% methanol aqueous solution, continue to heat up, the temperature rise rate is 10°C / h, stop the temperature rise when the temperature rises to 220°C, and continue to use the liquid space velocity for 1.2h -1 A 2% aqueous methanol solution ...
Embodiment 3
[0027] Add 60ml methanol steam reforming hydrogen production catalyst in the gas phase reactor, the weight percentage of copper oxide in the catalyst is 60%, the vaporization part of the device, the reaction part heats up simultaneously, the temperature rise rate is 20 ℃ / h, simultaneously with the gas space velocity 1000h -1 Air is fed in, and when the temperature rises to 120°C, the air is stopped; this step can also be fed inert gas, such as helium, neon or argon, etc. Then use a metering pump at an air-space velocity of 1000h -1 Pass into deionized water, and pass through to account for the volume percentage of both to be 0.5% of H 2 , the heating rate is 10°C / h. Stop feeding H when the temperature rises to 180°C 2 and water, and use a metering pump at a liquid space velocity of 0.8h -1 Pass in 0.5% methanol aqueous solution, continue to heat up at a rate of 10°C / h, stop heating when the temperature rises to 230°C, and continue at a liquid space velocity of 0.8h -1 A 1...
PUM
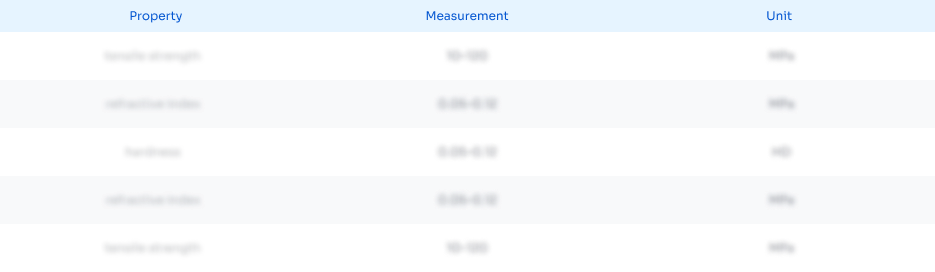
Abstract
Description
Claims
Application Information

- R&D
- Intellectual Property
- Life Sciences
- Materials
- Tech Scout
- Unparalleled Data Quality
- Higher Quality Content
- 60% Fewer Hallucinations
Browse by: Latest US Patents, China's latest patents, Technical Efficacy Thesaurus, Application Domain, Technology Topic, Popular Technical Reports.
© 2025 PatSnap. All rights reserved.Legal|Privacy policy|Modern Slavery Act Transparency Statement|Sitemap|About US| Contact US: help@patsnap.com