Process for manufacturing rare earth high-carbon low-alloy steel liner
A low-alloy steel, production process technology, applied in metal processing equipment, manufacturing tools, casting and molding equipment, etc., can solve the problems of easy breakage of linings, poor wear resistance, and broken fastening bolts. Strong abrasiveness and easy installation
- Summary
- Abstract
- Description
- Claims
- Application Information
AI Technical Summary
Problems solved by technology
Method used
Examples
Embodiment Construction
[0059] A rare-earth high-carbon low-alloy steel liner production process, including molding process, smelting process and heat treatment process;
[0060] The molding process includes a wet sand molding process and an EPC lost foam molding process, and the steps of the wet sand molding process are as follows:
[0061] Sand mixing section:
[0062](1) The surface sand material is 40--100 mesh or 50-100 mesh artificial quartz sand, the silicon content is not less than 98%, and the back sand is river sand;
[0063] (2), material ratio: quartz sand: 100%, bentonite: 7%, water: 5%;
[0064] (3) The sand mixing time should not be less than 8 minutes;
[0065] The so-called green sand molding process:
[0066] (1), the work site must be cleaned up before operation, and the preparations before production must be done;
[0067] (2) Sand loading: Put the sand box formwork in place and then fill it with sand, cover the formwork and model by 20-40 mm, fix the sand by hand, and then fi...
PUM
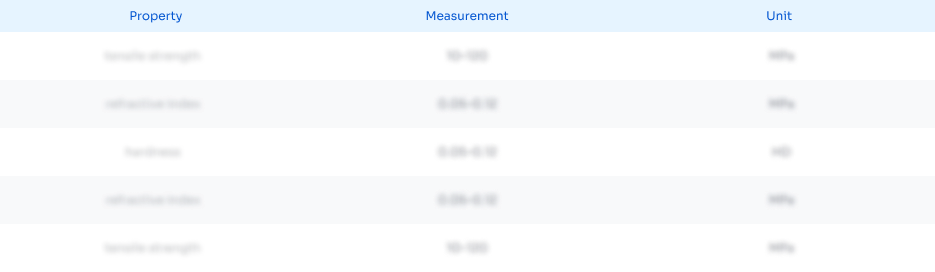
Abstract
Description
Claims
Application Information

- R&D Engineer
- R&D Manager
- IP Professional
- Industry Leading Data Capabilities
- Powerful AI technology
- Patent DNA Extraction
Browse by: Latest US Patents, China's latest patents, Technical Efficacy Thesaurus, Application Domain, Technology Topic, Popular Technical Reports.
© 2024 PatSnap. All rights reserved.Legal|Privacy policy|Modern Slavery Act Transparency Statement|Sitemap|About US| Contact US: help@patsnap.com