3-degree-of-freedom 6-UPS tri-translational parallel robot
A 6-UPS, degree-of-freedom technology, applied in manipulators, program-controlled manipulators, manufacturing tools, etc., can solve the problems of redundant self-motion, small working space, bending moment, etc.
- Summary
- Abstract
- Description
- Claims
- Application Information
AI Technical Summary
Problems solved by technology
Method used
Image
Examples
Embodiment 1
[0013] figure 1 It is a mechanical synchronously driven three-degree-of-freedom 6-UPS three-moving parallel robot disclosed in the present invention. Three pairs of linear drive branches are connected to the upper platform 1 and the base 2, and the three pairs of linear drive branches are positively connected between the upper platform 1 and the base 2. Triangular symmetrical distribution; each pair of linear drive branches includes two SPU type synchronous telescopic drive branches with the same structure, each SPU type branch has a ball pair at the upper end, a moving pair in the middle, and a universal pair at the lower end. The distance between the two ball pairs 3 of the branches is equal to the distance between the vertical axes 9 of the two universal joints. The upper end of each nut sleeve 4 is connected with the upper platform 1 by a ball pair 3, and the side surfaces of the lower ends of the two nut sleeves 4 are connected with the connecting rod 5 by two pin shafts ...
Embodiment 2
[0015] image 3 It is a hydraulic synchronously driven three-degree-of-freedom 6-UPS three-moving parallel robot disclosed in the present invention. Three pairs of linear drive branches are symmetrically distributed in an equilateral triangle between the upper platform 1 and the machine base 2; each pair of linear drive branches includes two structural forms The same size as the SPU type hydraulic synchronous telescopic drive branch, each SPU type branch has a ball pair at the upper end, a moving pair in the middle, and a universal pair at the lower end to connect with the machine base 2, and the moving pair is composed of a hydraulic cylinder 14 and a piston. 15 constitutes a hydraulic synchronous telescopic drive mechanism, the hydraulic cylinder 14 is connected with the upper platform 1 with the ball pair 3, the two hydraulic cylinders 14 are connected with the connecting rod 5 with two pins 6, the piston rod 15 is connected with the horizontal shaft 8 in rotation, and the h...
PUM
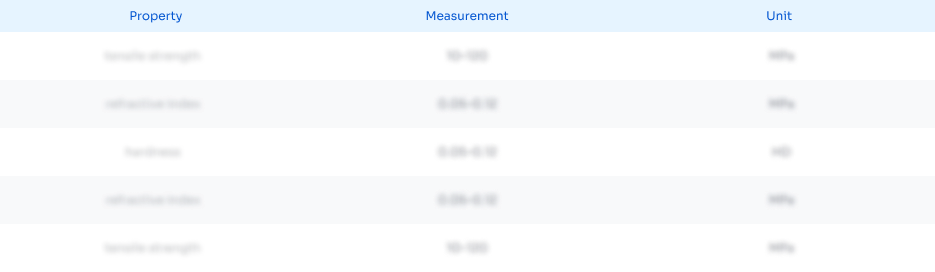
Abstract
Description
Claims
Application Information

- R&D
- Intellectual Property
- Life Sciences
- Materials
- Tech Scout
- Unparalleled Data Quality
- Higher Quality Content
- 60% Fewer Hallucinations
Browse by: Latest US Patents, China's latest patents, Technical Efficacy Thesaurus, Application Domain, Technology Topic, Popular Technical Reports.
© 2025 PatSnap. All rights reserved.Legal|Privacy policy|Modern Slavery Act Transparency Statement|Sitemap|About US| Contact US: help@patsnap.com