Method for separating and extracting iron, vanadium and titanium from vanadium-titanium magnetite
A technology for vanadium titanomagnetite and molten iron, which is applied in the field of separation and extraction of iron, vanadium and titanium, can solve the problems of long production process, high consumption of sodiumizing agent, large consumption of acid solution, etc., and achieves fast reaction speed and comprehensive recovery. High utilization effect
- Summary
- Abstract
- Description
- Claims
- Application Information
AI Technical Summary
Problems solved by technology
Method used
Examples
Embodiment 1
[0021] Vanadium titanium magnetite powder (main components are: TFe content is 55.90%, FeO content is 23.28%, TiO 2 The content is 11.84%, V 2 o 5 content of 0.73%), coal powder (the main components are: ash content of 11.25%, volatile matter content of 8.62%, carbon content of 80.19%, the amount of coal powder is 22% of mineral powder), bentonite (amount of mineral powder 3%) to form a 30mm pellet after mixing. Dry at 200°C until the moisture content of the pellets is 1%. Put it into a reduction furnace at 1400°C for 50 minutes and keep the PCO / PCO in the furnace 2 1.0, the metallization rate of iron reaches 94%, and the reduction degree of vanadium reaches 92%. The metallized pellets are put into an electric furnace for melting, and the melting temperature is 1600°C to obtain vanadium-containing molten iron and titanium-containing steel slag. The main components of vanadium-containing molten iron are: C content 0.02%, V content 0.67%, Ti content 0.05%, the main componen...
Embodiment 2
[0023] Vanadium titanium magnetite powder (main components are: TFe content is 54.40%, FeO content is 33.19%, TiO 2 The content is 15.92%, V 2 o 5 content of 0.55%), coal powder (the main components are: ash content of 15.72%, volatile matter of 12.44%, fixed carbon content of 71.84%, the amount of coal powder is 25% of mineral powder), carboxymethyl cellulose (amount of 0.3% of the mineral powder) to form a 3mm pellet after mixing. Dry at 350°C until the moisture content of the pellets is 0.5%. Put it into a reduction furnace at 1500°C for 5 minutes and keep the PCO / PCO in the furnace 2 0.3, the metallization rate of iron reaches 97%, and the reduction degree of vanadium reaches 94%. The metallized pellets are put into an electric furnace for melting, and the melting temperature is 1560°C to obtain vanadium-containing molten iron and titanium-containing steel slag. The main components of vanadium-containing molten iron are: C content of 0.018%, V content of 0.56%, and Ti...
Embodiment 3
[0025] Vanadium titanium magnetite powder (main components are: TFe content is 52.50%, FeO content is 30.72%, TiO 2 The content is 13.14%, V 2 o 5 content of 0.58%), electrode blocks (the main components are: fixed carbon content of 91.88%, the dosage is 15% of the mineral powder), carboxymethyl cellulose (the dosage is 0.3% of the mineral powder) and mixed to form a 15mm pellet . Dry at 280°C until the moisture content of the pellets is 0.7%. Put it into a reduction furnace at 1450°C for 30 minutes and keep the PCO / PCO in the furnace 2 2.0, the metallization rate of iron reaches 95%, and the reduction degree of vanadium reaches 92%. The metallized pellets are put into a submerged arc furnace for melting, and the melting temperature is 1700°C to obtain vanadium-containing molten iron and titanium-containing steel slag. The main components of vanadium-containing molten iron are: C content of 0.033%, V content of 0.48%, and Ti content of 0.035%. The main components of titan...
PUM
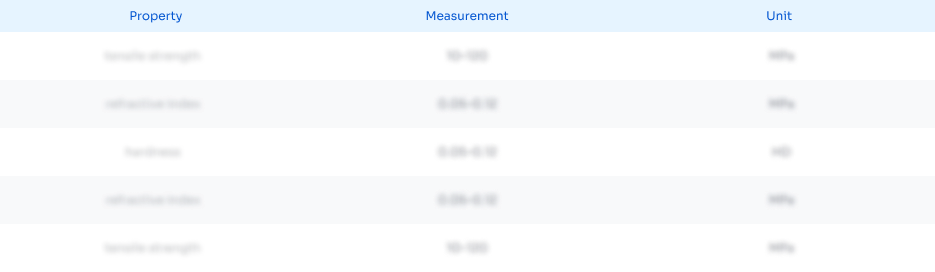
Abstract
Description
Claims
Application Information

- R&D
- Intellectual Property
- Life Sciences
- Materials
- Tech Scout
- Unparalleled Data Quality
- Higher Quality Content
- 60% Fewer Hallucinations
Browse by: Latest US Patents, China's latest patents, Technical Efficacy Thesaurus, Application Domain, Technology Topic, Popular Technical Reports.
© 2025 PatSnap. All rights reserved.Legal|Privacy policy|Modern Slavery Act Transparency Statement|Sitemap|About US| Contact US: help@patsnap.com