Inorganic electroluminescent display and its manufacturing method
A luminescent and display technology, which is applied in the direction of circuits, electrical components, semiconductor devices, etc., can solve the problems of reducing the withstand voltage performance of devices, low dielectric constant of the dielectric layer, and increased leakage, so as to reduce the requirements of the environment and equipment, and improve Brightness and overall efficiency, effects of reducing leakage and dielectric loss
- Summary
- Abstract
- Description
- Claims
- Application Information
AI Technical Summary
Problems solved by technology
Method used
Image
Examples
Embodiment 1
[0073] Embodiment 1. The lower electrode adopts a 150nm thick ITO electrode, the lower dielectric layer adopts 100nm strontium titanate, the light-emitting layer adopts 600nm manganese-doped zinc sulfide, and the upper dielectric layer adopts a composite of 300nm strontium titanate and 300nm tantalum pentoxide film, and the upper electrode is a 150nm aluminum electrode deposited by sputtering. The sputtering condition of the lower dielectric layer strontium titanate: the background vacuum is 4.0×10 -3 Pa, Ar / O 2 The ratio is 4:1, the sputtering pressure is 1.7 Pa, the substrate temperature is 500° C., the target base distance is 5 cm, the sputtering power is 400 W, and the sputtering time is 10 minutes. The light-emitting layer ZnS:Mn is deposited by electron beam evaporation, the substrate temperature is 173°C, and the background vacuum is 3.7×10 -3 Pa. The sputtering process of the strontium titanate layer in the upper dielectric layer is: the background vacuum is 1.4×10 ...
Embodiment 2
[0074] Embodiment 2, the lower electrode adopts a 150nm thick ITO electrode, the lower dielectric layer adopts 200nm strontium titanate, the light-emitting layer adopts 600nm manganese-doped zinc sulfide, and the upper dielectric layer adopts a composite of 200nm strontium titanate and 400nm tantalum pentoxide film, the upper electrode is a 150nm aluminum electrode. The sputtering condition of the lower dielectric layer strontium titanate: the background vacuum is 8.3×10 -4 Pa, Ar / O 2 The ratio is 4:1, the sputtering pressure is 1.3 Pa, the substrate temperature is 530° C., the target base distance is 5 cm, the sputtering power is 400 W, and the sputtering time is 9 minutes. The light-emitting layer ZnS:Mn is deposited by electron beam evaporation, the substrate temperature is 165°C, and the background vacuum is 2.6×10 -3 Pa. The sputtering condition of strontium titanate in the upper dielectric layer is: the background vacuum is 8.3×10 -3 Pa, Ar / O 2 The ratio is 3:2, the...
Embodiment 3
[0075] Embodiment 3. The lower electrode is made of 150nm thick ITO electrode, the lower dielectric layer is made of 200nm strontium titanate, the light-emitting layer is made of 600nm manganese-doped zinc sulfide, and the upper dielectric layer is made of 200nm strontium titanate and 500nm tantalum pentoxide. film, and the upper electrode is a 150nm aluminum electrode deposited by sputtering. The sputtering condition of the lower dielectric layer strontium titanate: the background vacuum is 8.4×10 -4 Pa, Ar / O 2 The ratio is 4:1, the sputtering pressure is 1.3 Pa, the substrate temperature is 550° C., the target base distance is 5 cm, the sputtering power is 400 W, and the sputtering time is 20 minutes. The light-emitting layer ZnS:Mn is deposited by electron beam evaporation, the substrate temperature is 165°C, and the background vacuum is 1.8×10 -3 Pa. Before sputtering the upper dielectric layer of strontium titanate, the sample was annealed in the sputtering chamber at ...
PUM
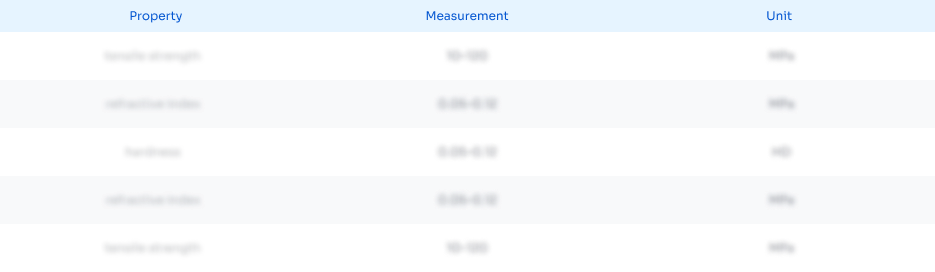
Abstract
Description
Claims
Application Information

- R&D
- Intellectual Property
- Life Sciences
- Materials
- Tech Scout
- Unparalleled Data Quality
- Higher Quality Content
- 60% Fewer Hallucinations
Browse by: Latest US Patents, China's latest patents, Technical Efficacy Thesaurus, Application Domain, Technology Topic, Popular Technical Reports.
© 2025 PatSnap. All rights reserved.Legal|Privacy policy|Modern Slavery Act Transparency Statement|Sitemap|About US| Contact US: help@patsnap.com