Elastic filament and processing method for drum dyeing of elastic yarn
An elastic yarn and elastic filament technology, applied in liquid/gas/vapor yarn/filament processing and other directions, can solve the problems of dark yarn color, loss of yarn elasticity, serious wool, etc., and achieve yarn elasticity Even, improve permanent recovery elasticity, smooth surface effect
- Summary
- Abstract
- Description
- Claims
- Application Information
AI Technical Summary
Problems solved by technology
Method used
Image
Examples
Embodiment 1
[0021] Elastic filament and elastic yarn are the processing method of natural or regenerated cellulose fiber yarn, the long filament of regenerated cellulose fiber coating spandex filament or PTT filament cylinder dyeing, and it comprises the following steps:
[0022] 1-1. Adopt the method of loose winding and reduce the winding density, so that the elastic filament or elastic yarn 1 is loosely wound on the smooth paper tube 2. The diameter of the winding paper tube 2 is 85mm. The density is 0.32g / cm 3 , winding line speed 5.5m / s;
[0023] 1-2. The yarn 1 formed by loose winding is covered with mesh fabric to prevent the yarn from being too loose and slipping;
[0024] 1-3. Under the action of pressure, press the mesh plastic tube 3 used for dyeing the yarn into the paper core, change the diameter of the plastic tube 3 to 60mm, and use the paper tube withdrawal device 4 to withdraw the wound paper tube 2, There is a gap 5 between the bobbin 1 and the plastic tube 3, such as ...
Embodiment 2
[0030] Wool, cashmere, milk fiber yarn and their blended yarns are coated with spandex filament or PTT filament, the loose winding speed is 5m / s, and the winding density is 0.34g / cm 3 1. The diameter of the winding paper tube is 85mm, and the diameter of changing the plastic tube is 60mm, and other processes are the same as in embodiment 1
Embodiment 3
[0032] Spandex filament or PTT filament coated with flax, ramie yarn and their blended yarn, loose winding speed is 7m / s, winding density is 0.33g / cm 3 , the diameter 85mm of winding paper tube, change the diameter 60mm of plastic tube, other technology is the same with embodiment 1.
PUM
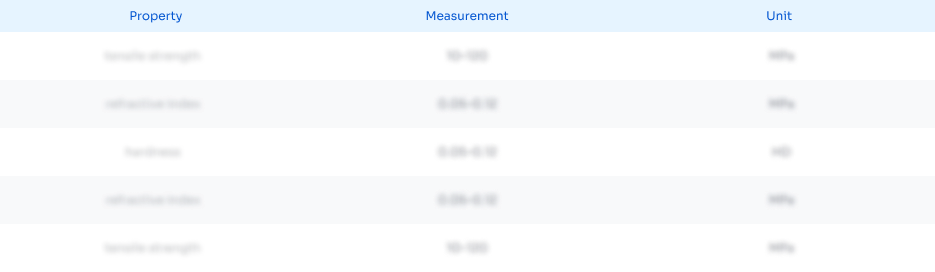
Abstract
Description
Claims
Application Information

- R&D
- Intellectual Property
- Life Sciences
- Materials
- Tech Scout
- Unparalleled Data Quality
- Higher Quality Content
- 60% Fewer Hallucinations
Browse by: Latest US Patents, China's latest patents, Technical Efficacy Thesaurus, Application Domain, Technology Topic, Popular Technical Reports.
© 2025 PatSnap. All rights reserved.Legal|Privacy policy|Modern Slavery Act Transparency Statement|Sitemap|About US| Contact US: help@patsnap.com