Fluorocarbon elastomer latex and its preparation method
An elastomer and fluorocarbon technology, which is applied in the field of fluorocarbon elastomer emulsion and its preparation, can solve the problems of affecting the decorative protective effect of coatings, poor stain resistance of elastic exterior wall coatings, and poor weather resistance of latex films.
- Summary
- Abstract
- Description
- Claims
- Application Information
AI Technical Summary
Problems solved by technology
Method used
Image
Examples
Embodiment 1
[0021] In a four-necked flask with a condenser, a dropping device, a stirrer, and a thermometer, add 150 grams of deionized water, 3.5 grams of methacrylamide isopropyl sulfonate, and 1.85 grams of nonylphenol polyoxyethylene ether, Sodium bicarbonate 0.27 g. After fully dissolving, heat up to 75-80°C. After 5 minutes, 15.0 grams of methyl methacrylate, 12.5 grams of methacrylic acid, 135.0 grams of butyl acrylate, 27.5 grams of isobornyl methacrylate, 47.5 grams of hexafluorobutyl acrylate, and 1.5 grams of NP-40 were added dropwise. 1.5 grams of nonylphenol polyoxyethylene ether, 2.0 grams of N-methylolacrylamide, the monomer pre-emulsion prepared by the mixture of 50.0 grams of deionized water, while adding 1.75 grams of ammonium persulfate (dissolved in 50.0 grams of deionized water) deionized water) in aqueous solution. The addition was completed in 2.5-3 hours, and the reaction was carried out at 80°C for 2 hours. Add 0.2 g of tert-butyl hydroperoxide (dissolved in 5 ...
Embodiment 2
[0023] In a four-neck flask equipped with a condenser, dropping device, stirrer, and thermometer, add 150 grams of deionized water, 3.6 grams of methacrylsulfonate, 1.8 grams of octylphenol polyoxyethylene ether, and sodium bicarbonate 0.45 grams. After fully dissolving, heat up to 75-80°C. After 5 minutes, 35 grams of methyl methacrylate, 10.0 grams of acrylic acid, 120 grams of butyl acrylate, 10.0 grams of isobornyl acrylate, 15 grams of dodecafluoroheptyl acrylate, 30.0 grams of hexafluorobutyl acrylate, 4.0 N-methylol acrylamide, 1.5 grams of octylphenol polyoxyethylene ether, 3.0 grams of sodium methacryl sulfonate, monomer pre-emulsion prepared from a mixture of 50.0 grams of deionized water, while adding persulfuric acid dropwise Ammonium 1.5 g (dissolved in 35 g deionized water) in water. The addition was completed in 2.5-3 hours, and the reaction was carried out at 80°C for 2 hours. Add 0.25 grams of tert-butyl hydroperoxide (dissolved in 5 grams of deionized wate...
Embodiment 3
[0025] In a four-necked flask equipped with a condenser, a dropping device, an agitator, and a thermometer, add 125 grams of deionized water, 3.59 grams of methacrylamide isopropyl sulfonate, 1.915 grams of fatty alcohol polyoxyethylene ether, carbonic acid Sodium hydrogen 0.20 g. After fully dissolving, heat up to 75-80°C. After 5 minutes, 52.50 grams of methyl methacrylate, 12.67 grams of methacrylic acid, 100.0 grams of butyl acrylate, 22.5 grams of isobornyl methacrylate, 47.5 grams of dodecafluoroheptyl acrylate, and N-methylol 3.0 grams of acrylamide, 1.5 grams of NP-40, 1.5 grams of octylphenol polyoxyethylene ether, the monomer pre-emulsion prepared by the mixture of 51.5 grams of deionized water, while adding 1.8 grams of ammonium persulfate (dissolved in 50 grams in deionized water). The addition was completed in 2.5-3 hours, and the reaction was carried out at 80°C for 2 hours. Add 0.2 grams of tert-butyl hydroperoxide (dissolved in 5 grams of deionized water), c...
PUM
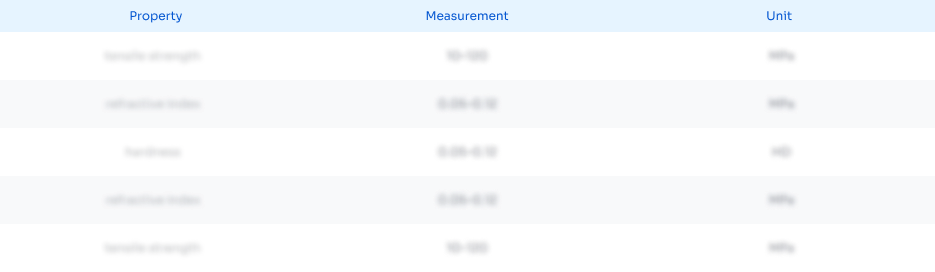
Abstract
Description
Claims
Application Information

- R&D Engineer
- R&D Manager
- IP Professional
- Industry Leading Data Capabilities
- Powerful AI technology
- Patent DNA Extraction
Browse by: Latest US Patents, China's latest patents, Technical Efficacy Thesaurus, Application Domain, Technology Topic, Popular Technical Reports.
© 2024 PatSnap. All rights reserved.Legal|Privacy policy|Modern Slavery Act Transparency Statement|Sitemap|About US| Contact US: help@patsnap.com