Hot compressing link method of polymer microfluid system
A microfluidic system and thermocompression bonding technology, applied in the field of thermocompression bonding of polymer microfluidic systems, can solve problems such as reducing the glass transition temperature of the polymer surface, shorten the bonding time and solve the bonding strength. Problems, the effect of simple craftsmanship
- Summary
- Abstract
- Description
- Claims
- Application Information
AI Technical Summary
Problems solved by technology
Method used
Examples
Embodiment 1
[0013] Example 1. Bonding of polymethylmethacrylate (PMMA) microfluidic systems
[0014] 1) Cleaning and drying of PMMA flakes
[0015] Take two 2mm thick PMMA sheets, one contains microstructure graphics, and its surface flatness is less than 1 micron, and the other does not contain graphics, and the size is 5cm×5cm. First clean the two PMMA sheets with ethanol, then wash them with deionized water, then put the two PMMA sheets in an oven for 4 hours at 80°C, and finally store them in a drying oven.
[0016] 2) Surface modification of PMMA flakes
[0017] Put the PMMA sheet without microstructure pattern on the glue spinner, add the polymer monomer methyl methacrylate (MMA) dropwise on the sheet, spin coating at 1000 rpm for 10 seconds.
[0018] MMA can dissolve PMMA, but it is not a good solvent for PMMA. If the surface smoothness of the PMMA containing the microstructure is better, the surface modification of the PMMA flakes can be carried out by using the spin coating me...
Embodiment 2
[0025] Example 2. Bonding of polymethylmethacrylate (PMMA) microfluidic systems
[0026] 1) Cleaning and drying of PMMA flakes
[0027] Take two 2mm thick PMMA sheets, one contains microstructure graphics, and its surface flatness is greater than 1 micron, and the other does not contain graphics, and the size is 5cm×5cm. First clean the two PMMA sheets with ethanol, then wash them with deionized water, then put the two PMMA sheets in an oven for 4 hours at 80°C, and finally store them in a drying oven.
[0028] 2) Surface modification of PMMA flakes
[0029] Add the polymer monomer MMA into the glass container, then put the PMMA sheet without microstructure pattern into the MMA, take it out after 1 minute, and blow off the MMA attached to the surface with nitrogen.
[0030] MMA can dissolve PMMA, but it is not a good solvent for PMMA. If the surface smoothness of PMMA containing microstructure is not good, the surface modification of PMMA flakes can be carried out by impreg...
Embodiment 3
[0035] Example 3. Bonding of polystyrene (PS) microfluidic systems
[0036] 1) Cleaning and drying of PS flakes
[0037] Take two 2mm thick PS slices, one contains microstructure graphics, and its surface unevenness is less than 1 micron, and the other does not contain graphics, both of which are 5cm×5cm in size. First clean the two PS sheets with ethanol, then wash them with deionized water, then put the two PS sheets in an oven at 75°C for 4 hours, and finally put them in a drying oven for storage.
[0038] 2) Surface modification of PS flakes
[0039] Add the polymer monomer styrene into the glass container, then heat the PS sheet without microstructure pattern to 75°C, put it into the glass container, put it in the steam of styrene for 5 minutes, and then take it out.
[0040]Styrene is a good solvent for PS. If spin coating method or dipping method is used to modify the surface of PS flakes, too much styrene may be added to the surface of PS, so steam method is more app...
PUM
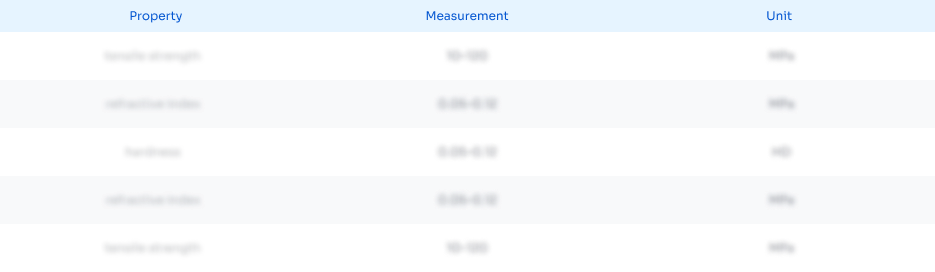
Abstract
Description
Claims
Application Information

- Generate Ideas
- Intellectual Property
- Life Sciences
- Materials
- Tech Scout
- Unparalleled Data Quality
- Higher Quality Content
- 60% Fewer Hallucinations
Browse by: Latest US Patents, China's latest patents, Technical Efficacy Thesaurus, Application Domain, Technology Topic, Popular Technical Reports.
© 2025 PatSnap. All rights reserved.Legal|Privacy policy|Modern Slavery Act Transparency Statement|Sitemap|About US| Contact US: help@patsnap.com