Method for displacably guiding a displaceable machine element of a numerically controlled tool machine or production machine
A technology for moving machines and machine parts, applied in the field of motion guidance, can solve problems such as long processing time and lack of optimal utilization of dynamic performance, and achieve the effect of short processing time
- Summary
- Abstract
- Description
- Claims
- Application Information
AI Technical Summary
Problems solved by technology
Method used
Image
Examples
Embodiment Construction
[0064] The method of the present invention is shown in the form of a structural block diagram in FIG. 4. First, the support point is defined in the function block 28.
[0065] This is generally based on Figure 6 , Use the spatial lattice to divide the working space 31 of the machine tool, and carry out the movement process of the machine parts in the machine tool. Figure 6 Shows a linear distribution. Of course, it can also be any other lattice form and distribution. Especially in positions that are important for motion guidance, it is meaningful to match the density of the support points around the motion track S. The support points are at the nodes of the dot matrix line segment, for clarity only Figure 6 A support point 32 is shown in. Here, a spatial lattice that becomes a planar lattice is used in the two-axis machine tool used in the embodiment (only a two-dimensional motion track S).
[0066] Then, in the function block 21, the machine part 8 is used to activate the firs...
PUM
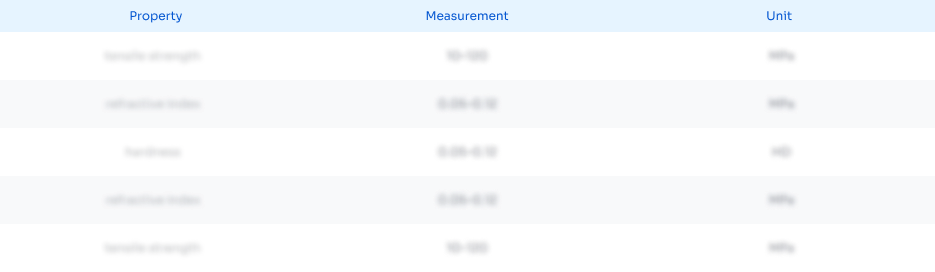
Abstract
Description
Claims
Application Information

- R&D Engineer
- R&D Manager
- IP Professional
- Industry Leading Data Capabilities
- Powerful AI technology
- Patent DNA Extraction
Browse by: Latest US Patents, China's latest patents, Technical Efficacy Thesaurus, Application Domain, Technology Topic, Popular Technical Reports.
© 2024 PatSnap. All rights reserved.Legal|Privacy policy|Modern Slavery Act Transparency Statement|Sitemap|About US| Contact US: help@patsnap.com