Method of coating lubricant in metallic injection machine
一种注射成形机、分型剂的技术,应用在在金属注射成形机中涂覆分型剂领域,能够解决增加维修频率、操作环境退化、模制件质量下降等问题,达到简化模具结构的效果
- Summary
- Abstract
- Description
- Claims
- Application Information
AI Technical Summary
Problems solved by technology
Method used
Image
Examples
Embodiment Construction
[0019] A metal element itself having a melting point equal to or lower than 700° C. or an alloy based on the metal is referred to as a metal raw material of the present invention. As practical examples, for example aluminium, magnesium, zinc, tin, lead, bismuth, terbium and similar elements may be chosen, in particular aluminium, magnesium, lead, zinc, bismuth, tin itself and alloys based on these metals are preferred. Any metal raw material is a metal element or alloy that can be melted in a heating cylinder by heat supplied from the outside and shaped by injection into a mold product cavity. Although the melting point of copper is 1085°C and much higher than 700°C, the melting point of copper alloys such as copper alloys used for brazing is equal to or less than 700°C, and copper alloys also constitute objects of metal raw materials according to the present invention. Furthermore, according to the invention, the object of the invention is also achieved by simultaneously addi...
PUM
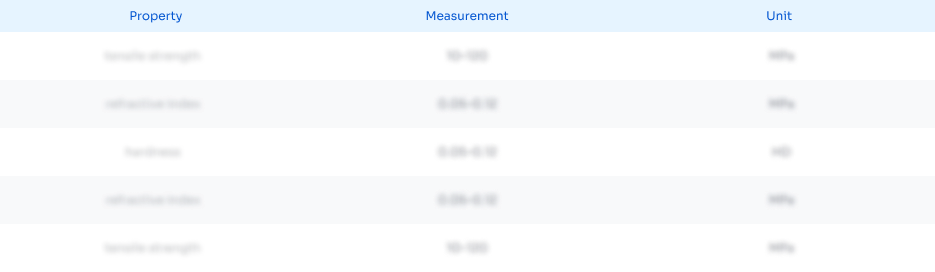
Abstract
Description
Claims
Application Information

- R&D
- Intellectual Property
- Life Sciences
- Materials
- Tech Scout
- Unparalleled Data Quality
- Higher Quality Content
- 60% Fewer Hallucinations
Browse by: Latest US Patents, China's latest patents, Technical Efficacy Thesaurus, Application Domain, Technology Topic, Popular Technical Reports.
© 2025 PatSnap. All rights reserved.Legal|Privacy policy|Modern Slavery Act Transparency Statement|Sitemap|About US| Contact US: help@patsnap.com