Thread cutting insert
A thread cutting and blade technology, applied in cutting blades, thread cutting tools, tools for lathes, etc., can solve the problems of high-frequency vibration, increased cutting resistance, and reduced surface precision of finishing, and achieve the purpose of suppressing the increase of resistance big effect
- Summary
- Abstract
- Description
- Claims
- Application Information
AI Technical Summary
Problems solved by technology
Method used
Image
Examples
Embodiment Construction
[0036] Figure 1 to Figure 14 An embodiment of the present invention is shown. In this embodiment, the insert body 1 is made of a hard material such as cemented carbide, such as figure 2 As shown in the flat shape forming a roughly equilateral triangle, in the center of the upper and lower surfaces constituting a roughly equilateral triangle, there are openings along the thickness direction ( figure 1 , 3 Up and down directions in ~5. Hereinafter referred to as the blade thickness direction) through the circular mounting hole 2 of the blade main body 1 , the blade main body 1 is a 120° rotationally symmetrical shape about the center line O of the mounting hole 2 . Also, in a plan view along the center line O, the corners of the above-mentioned equilateral triangle formed by the blade body 1 are as follows: figure 2 As shown, a cut is made in a manner substantially perpendicular to one of the edge parts intersecting at the corner, and at the part of the cut, as Image 6 ...
PUM
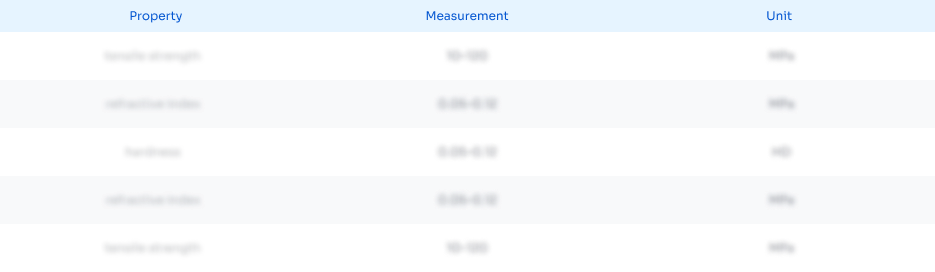
Abstract
Description
Claims
Application Information

- Generate Ideas
- Intellectual Property
- Life Sciences
- Materials
- Tech Scout
- Unparalleled Data Quality
- Higher Quality Content
- 60% Fewer Hallucinations
Browse by: Latest US Patents, China's latest patents, Technical Efficacy Thesaurus, Application Domain, Technology Topic, Popular Technical Reports.
© 2025 PatSnap. All rights reserved.Legal|Privacy policy|Modern Slavery Act Transparency Statement|Sitemap|About US| Contact US: help@patsnap.com