Process for dry coke quenching and coke desulfurating by coke oven gas
A technology of dry quenching and coke, applied in the cooling of coke, coke oven, petroleum industry, etc., can solve the problem of no coke desulfurization, unable to obtain lump coke, etc.
- Summary
- Abstract
- Description
- Claims
- Application Information
AI Technical Summary
Problems solved by technology
Method used
Image
Examples
example 1
[0029] Load 5kg of coke from a factory in a small vertical straight tube quenching chamber reactor, the sulfur content of the coke is 0.71%, heat the reactor, stop heating when the temperature reaches the actual coke oven discharge temperature of 1000°C, and The simulated coke oven gas at normal temperature (about 25°C) is supplied from the bottom of the reactor to cool the red hot coke, wherein the components of the coke oven gas (all gas components in the examples are by volume percentage) are about 55% H2-25% CH4-15% CO-5% N2, the gas supply rate is 50L / min, until the furnace temperature drops to 200°C, the gas supply is stopped. The cooling process of the test took 160 minutes, and the average sulfur content of the coke analyzed after the test was 0.45%. However, under the same conditions, nitrogen gas was introduced for test comparison, and the cooling process took about 190 minutes, and the average sulfur content of the coke was 0.70%. After the coal gas was introduced,...
example 2
[0031] The simulated coke oven gas 55%H blown into in Example 1 2 -25%CH 4 -15%CO-5%N 2 Change to natural gas and repeat the test of Example 1. The main components of natural gas are: 93.38% CH 4 -2.68%N 2 -1.86%CO 2 -1.67%C 2 h 6 . The cooling time of the test was 110 minutes, and the average sulfur content of the coke analyzed after the test was 0.50%. Compared with the blank test with nitrogen gas under the same conditions, the sulfur content of coke was reduced by 30% and the cooling time was reduced by 42% after gas was fed.
example 3
[0033] The simulated coke oven gas 55%H blown into in Example 1 2 -25%CH 4 -15%CO-5%N 2 Change to H 2 , repeating the test of Example 1, the average sulfur content of the coke analyzed after the test was 0.41%, and the cooling time was 205min. Compared with the corresponding blank test, the sulfur content of the coke was reduced by 42% and the cooling time was increased by 8% after the gas was introduced.
PUM
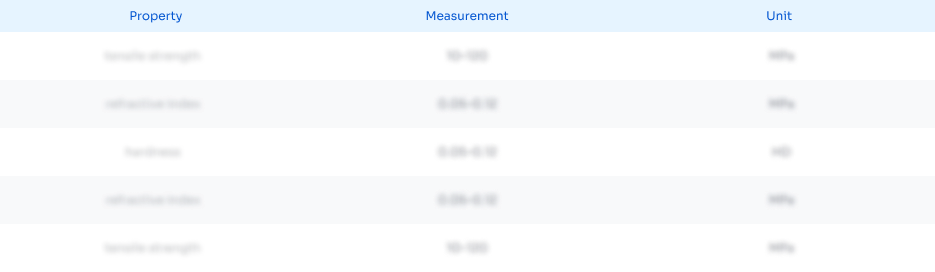
Abstract
Description
Claims
Application Information

- R&D
- Intellectual Property
- Life Sciences
- Materials
- Tech Scout
- Unparalleled Data Quality
- Higher Quality Content
- 60% Fewer Hallucinations
Browse by: Latest US Patents, China's latest patents, Technical Efficacy Thesaurus, Application Domain, Technology Topic, Popular Technical Reports.
© 2025 PatSnap. All rights reserved.Legal|Privacy policy|Modern Slavery Act Transparency Statement|Sitemap|About US| Contact US: help@patsnap.com