Prepn process of mixable silicon rubber structure controlling agent
A technology of silicone rubber and structurant, applied in the field of preparation of kneading silicone rubber anti-structural agent, can solve the problems of high yield of volatile components, cumbersome and energy-consuming post-processing, difficult solvent recovery, etc., and achieve excellent anti-structural agent. performance, improved tear strength, and easy handling
- Summary
- Abstract
- Description
- Claims
- Application Information
AI Technical Summary
Problems solved by technology
Method used
Image
Examples
Embodiment 1
[0027] The preparation of embodiment 1 mixing type silicone rubber anti-structural agent
[0028] Take 300g D 4 First carry out vacuum distillation to remove 15g of cyclic body and water, then add 60g of dimethyldimethoxysilane, stir evenly, heat up to 80°C, add 15g of granular activated clay (80 mesh), stir for 1 hour at constant temperature, and then slowly Slowly raise the temperature to 100°C and continue to stir and heat-retain for 3 hours, then cool down to 80°C, add 18g of water and heat-retain for 3 hours at 64°C, cool to room temperature, filter to remove activated clay, and distill the filtrate under reduced pressure to remove 30g of low-molecular substances, and finally obtain 310g Colorless, transparent liquid, the yield is 85%, and its viscosity is 11.5mm 2 / s, the hydroxyl content is 6.62% (mass percentage, the same below), and the methoxy content is 4.27%.
Embodiment 2
[0029] The preparation of embodiment 2 mixing type silicone rubber anti-structural agent
[0030] Take 300g D 4First carry out vacuum distillation to remove 15g of ring body and water, then add 58g of dimethyldiethoxysilane, stir evenly, then raise the temperature to 100°C, add 18g of cation exchange resin, stir and react at constant temperature for 1.5 hours, and then slowly raise the temperature to 110°C Continue to stir and keep warm for 3 hours at ℃, cool down to 90 ℃, add 21g of water at 78 ℃ and keep warm for 3 hours, cool to normal temperature, filter and remove activated clay, and obtain 340g of colorless, transparent liquid with a yield of 93% and a viscosity of 18.0 mm 2 / s, the hydroxyl content is 6.02%, and the ethoxy content is 3.86%.
Embodiment 3
[0031] Embodiment 3 Preparation of mixing type silicone rubber anti-structural agent
[0032] Take 300g of DMC and first carry out vacuum distillation to remove 15g of DMC and water, then add 60g of dimethyldimethoxysilane, stir evenly, heat up to 80°C, add 21g of activated clay (60 mesh), stir and react at constant temperature for 1 hour, and then Slowly raise the temperature to 100°C and continue to stir and keep warm for 3 hours, then cool down to 70°C, add 18g of water at 64°C and keep warm for 3 hours, then cool to normal temperature, filter to remove activated clay, and distill the filtrate under reduced pressure at 150°C (-0.1Mpa) Slough off 25g low-molecular matter, finally obtain 321g colorless, transparent liquid, yield 88%, and its viscosity is 13.5mm 2 / s, the hydroxyl content is 6.24% (mass percentage, the same below), and the methoxy content is 4.08%.
PUM
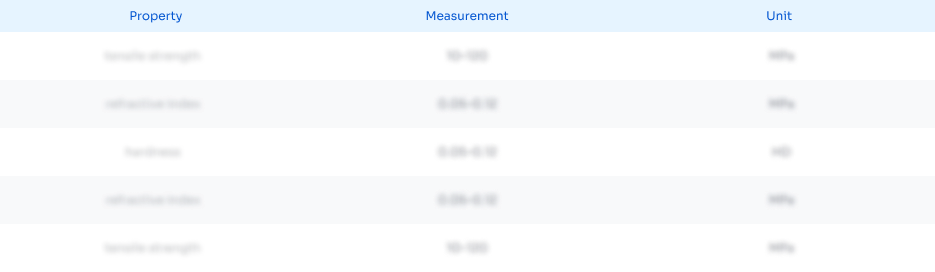
Abstract
Description
Claims
Application Information

- Generate Ideas
- Intellectual Property
- Life Sciences
- Materials
- Tech Scout
- Unparalleled Data Quality
- Higher Quality Content
- 60% Fewer Hallucinations
Browse by: Latest US Patents, China's latest patents, Technical Efficacy Thesaurus, Application Domain, Technology Topic, Popular Technical Reports.
© 2025 PatSnap. All rights reserved.Legal|Privacy policy|Modern Slavery Act Transparency Statement|Sitemap|About US| Contact US: help@patsnap.com