Method of preparing ZSM-5 using variable temperature without organic template
A technology of ZSM-5 and particle size distribution, applied in chemical instruments and methods, crystalline aluminosilicate zeolites, chemical/physical processes, etc., can solve problems such as long reaction time
- Summary
- Abstract
- Description
- Claims
- Application Information
AI Technical Summary
Problems solved by technology
Method used
Image
Examples
Embodiment approach
[0097] According to a first preferred embodiment of the present invention, a silicon dioxide source, an alkali metal oxide source (eg, alkali metal hydroxide) and water are mixed to prepare a first aqueous solution. Thus, it is desirable to control the amount of silica source in the first aqueous solution to be in the range of about 21.5-26.7% by weight. This is because silica cannot be uniformly dissolved in water if the amount of water in the first aqueous solution is too small or too large. A source of alumina, a source of alkali metal oxides and water are additionally mixed to obtain a second aqueous solution. In this way, the amount of alumina source in the second aqueous solution is controlled at about 0.9-4.4% by weight. This is also because the alumina source should be homogeneously dissolved in water. Then, the second aqueous solution is added to the first aqueous solution. Considering the concentrations of the first aqueous solution and the second aqueous solution...
Embodiment 1
[0117] Put 60 g of Ludox AS-40 as a silica source into beaker 1, slowly add 21.4 g of 10% by weight NaOH solution into the beaker while stirring at 200 rpm, then add 30 g of distilled water, and then stir at 200 rpm for 3 hours. Separately, 1.65 g of sodium aluminate powder, 48.8 g of distilled water, and 8.8 g of a 10% by weight NaOH solution were added to the beaker 2, and mixed for 3 hours using a magnetic stirrer. After that, the solution in beaker 2 and another 18.8 g of distilled water were slowly added to the solution in beaker 1, followed by mixing for 1 hour. Subsequently, the resulting mixture was transferred to a 300ml Teflon container by using a figure 1 In the autoclave with the sampling port shown, the reaction temperature was raised to 190° C. while stirring at 200 rpm, and kept for 2 hours. Then, the reaction temperature was cooled to 150°C and held for 40 hours. After completion of the reaction, the reaction product was filtered through a membrane filter wit...
Embodiment 2
[0121] Put 60 g of Ludox AS-40 as a silica source into beaker 1, slowly add 21.4 g of 10% by weight NaOH solution into the beaker while stirring at 200 rpm, then add 30 g of distilled water, and then stir at 200 rpm for 3 hours. 2.0 g of sodium aluminate powder, 49.4 g of distilled water and 7.5 g of 10% by weight NaOH solution were added to beaker 2 and mixed for 3 hours using a magnetic stirrer. After that, the solution in beaker 2 and another 19.4 g of distilled water were slowly added to the solution in beaker 1, followed by mixing for 1 hour. Subsequently, by using the same autoclave as in Example 1, the reaction temperature of the formed mixture was raised to 190° C. while stirring at 200 rpm, and maintained for 2 hours. Then, the reaction temperature was cooled to 150°C and held for 35 hours. After completion of the reaction, the properties of the formed reaction product were analyzed in the same manner as in Example 1. The results are shown in Figure 3a and 3b and...
PUM
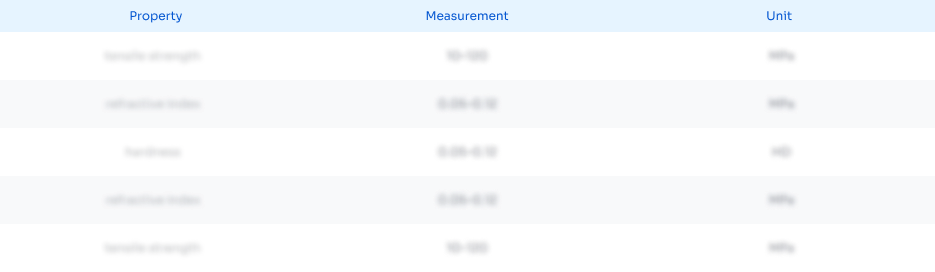
Abstract
Description
Claims
Application Information

- R&D Engineer
- R&D Manager
- IP Professional
- Industry Leading Data Capabilities
- Powerful AI technology
- Patent DNA Extraction
Browse by: Latest US Patents, China's latest patents, Technical Efficacy Thesaurus, Application Domain, Technology Topic, Popular Technical Reports.
© 2024 PatSnap. All rights reserved.Legal|Privacy policy|Modern Slavery Act Transparency Statement|Sitemap|About US| Contact US: help@patsnap.com