Sectional hoisting method
A process method and segmental hoisting technology, applied in the direction of transportation and packaging, load hanging components, etc., can solve the problems affecting the level of the superstructure, expensive production costs, unfavorable precise positioning, etc., to ensure the success rate, safe and reliable operation, The effect of high one-time placement rate
- Summary
- Abstract
- Description
- Claims
- Application Information
AI Technical Summary
Problems solved by technology
Method used
Image
Examples
Embodiment Construction
[0026] The present invention will be further described in detail below in conjunction with the accompanying drawings and specific embodiments.
[0027] figure 1 The shown embodiment 1 is the layout of the hoisting process method carried by the general section, specifically the hoisting process method of the superstructure, and the 6-story segments are hoisted together, and the net weight of each segment is 580 tons.
[0028] The configuration and connection of the slings are as follows: remove the hoisting bar of the two hooks 1# hook (1) and 2# hook (2) on the trolley, install the special 400-ton main hoisting bar (4), and then equip a 65mm-diameter There are 7 steel wires (6) with a length of 10m in total, 4 of which are drawn through the pulley and folded in half, and then one steel wire (6) with a diameter of 65mm and a length of 15m is folded in half and the other three steel wires (6) with a length of 10m are folded in half and connected to the bottom. There are 4 high-...
PUM
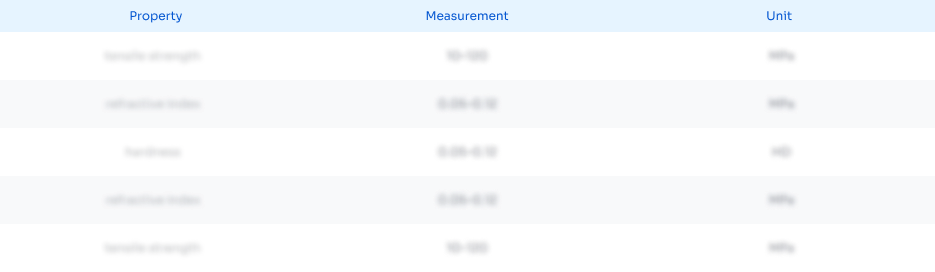
Abstract
Description
Claims
Application Information

- R&D
- Intellectual Property
- Life Sciences
- Materials
- Tech Scout
- Unparalleled Data Quality
- Higher Quality Content
- 60% Fewer Hallucinations
Browse by: Latest US Patents, China's latest patents, Technical Efficacy Thesaurus, Application Domain, Technology Topic, Popular Technical Reports.
© 2025 PatSnap. All rights reserved.Legal|Privacy policy|Modern Slavery Act Transparency Statement|Sitemap|About US| Contact US: help@patsnap.com