Catalytic cracking co-catalyst for producing diesel oil and its preparing method
A co-catalyst and catalytic cracking technology, which is applied in catalytic cracking, cracking, petroleum industry and other directions, can solve the problems of insufficient ability to increase diesel production, use, and cannot be used as a diesel auxiliary agent, etc., to increase the production of diesel components, increase dry gas production, The effect of total liquid recovery unchanged
- Summary
- Abstract
- Description
- Claims
- Application Information
AI Technical Summary
Problems solved by technology
Method used
Examples
Embodiment 1
[0039] (1) Preparation of in-situ crystallization product microspheres:
[0040] Add water to 10Kg (dry basis) kaolin produced in Suzhou to make a slurry with a solid content of 35%, and add 2% sodium silicate as a dispersant or binder, and spray to obtain 8.5Kg of spray microspheres. The sprayed microspheres were roasted in a muffle furnace at 920° C. for 3 hours to obtain roasted microspheres, which contained about 8% mullite. Sodium silicate (containing 19.84% SiO 2 , 6.98% Na 2 (2) 452mL, sodium hydroxide solution (containing 14% NaOH) 756mL, guiding agent (containing 11.65% SiO 2 , 1.32% Al 2 o 3 , 12.89% Na 2 (0) 97 mL, 57 mL of deionized water, and 1000 g of calcined microspheres were put into a stainless steel reactor, heated to 90° C. and crystallized at a constant temperature for 24 hours. After the crystallization is completed, the mother liquor is removed by filtration, and the filter cake is washed and dried to obtain crystallized product microspheres. As d...
Embodiment 2
[0050] (1) Preparation of crystallization product microspheres:
[0051] All the reaction materials are the same as in Example 1, wherein the roasting conditions of the sprayed microspheres are 1040°C and 0.5 hours, and 2000 mL of sodium silicate, 4052 mL of sodium hydroxide solution, 485 mL of directing agent, and 5000 g of roasted microspheres are put into the stainless steel reactor in turn under stirring. , the temperature was raised to 92°C and crystallized at constant temperature for 20 hours. X-ray diffraction determined that the crystallized product contained 18% NaY zeolite, and the zeolite silicon-aluminum ratio was 4.94.
[0052] (2) Post-treatment of in-situ crystallization products to prepare co-catalysts:
[0053] Ammonium salt primary exchange: add deionized water 2.5Kg in the stainless steel kettle, drop into in situ crystallization product 500g and ammonium nitrate 250g [ammonium nitrate / crystallization product (mass ratio)=0.20] prepared by the above-mention...
Embodiment 3
[0061] (1) Preparation of crystallization product microspheres:
[0062] All reaction raw materials are the same as in Example 1, wherein the roasting conditions of sprayed microspheres are 980°C and 2 hours, and 400 mL of sodium silicate, 600 mL of sodium hydroxide solution, 88 mL of directing agent, and 1000 g of roasted microspheres are put into the glass reactor in turn under stirring. , after crystallization at 95° C. for 32 hours, it was determined that the crystallized product contained 8% NaY zeolite, and the zeolite silicon-aluminum ratio was 5.54.
[0063] (2) Post-treatment of in-situ crystallization products to prepare co-catalysts:
[0064] One exchange of ammonium salt: add 4 kg of deionized water in a stainless steel kettle, drop into 800 g of in-situ crystallization product prepared by the above method and 240 g of ammonium sulfate [ammonium sulfate / crystallization product (mass ratio)=0.30] under stirring, at pH =3.0~3.5, exchange at 90°C for 1 hour, remove t...
PUM
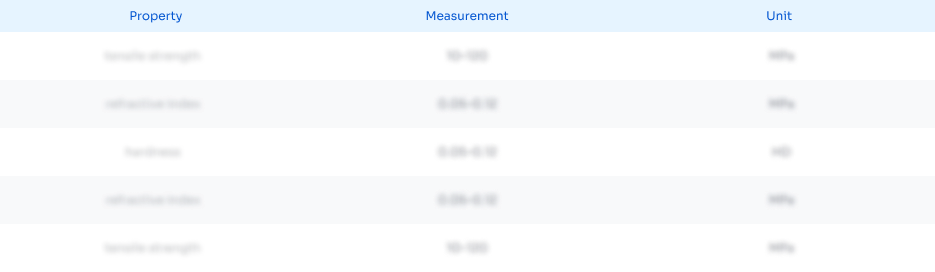
Abstract
Description
Claims
Application Information

- R&D
- Intellectual Property
- Life Sciences
- Materials
- Tech Scout
- Unparalleled Data Quality
- Higher Quality Content
- 60% Fewer Hallucinations
Browse by: Latest US Patents, China's latest patents, Technical Efficacy Thesaurus, Application Domain, Technology Topic, Popular Technical Reports.
© 2025 PatSnap. All rights reserved.Legal|Privacy policy|Modern Slavery Act Transparency Statement|Sitemap|About US| Contact US: help@patsnap.com