Convective method of heating glass sheets using compressed air in conjunction with heated oven air
A technology for compressed air and glass plates, applied in the field of semi-convective pressure/forced air systems, which can solve problems such as slow heat transfer and increased heating cycle time
- Summary
- Abstract
- Description
- Claims
- Application Information
AI Technical Summary
Problems solved by technology
Method used
Image
Examples
Embodiment Construction
[0020] Referring now to the drawings, FIG. 7 shows a spout 21 in rear view and FIG. 8 shows the spout 21 in front view. Compressed air enters the lance 21 through holes 23, furnace gas is drawn into the lance through upper ports 25, and the compressed air and furnace gas mix in a mixing chamber 26 in the lower part of the lance 21 to form a hot air mixture. This air mixture of compressed air and furnace gas is discharged through the lower port 27 onto the glass sheet S, thereby heating the glass sheet for further processing, such as tempering.
[0021] For ease of processing, the hole 23 has been optimized as a 30° inclined hole, but other angles can also be made. The diameter of the holes is 0.080mm, so particles formed inside the compressed air delivery system can be blown through these holes. The diameter of the holes can be varied as necessary or desired.
[0022] The upper port 25 is flared at the inner bell mouth 29 so that furnace gas can be sucked into the nozzle 21 ...
PUM
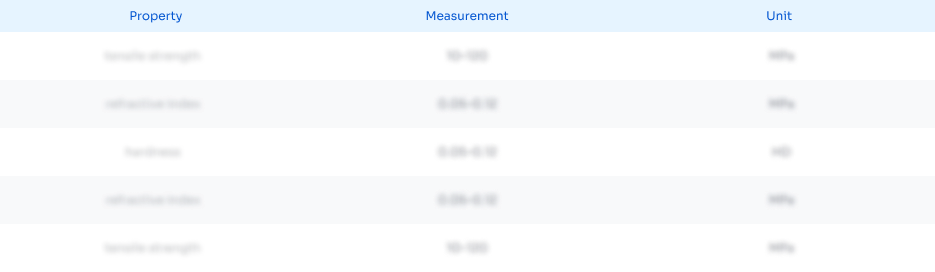
Abstract
Description
Claims
Application Information

- R&D
- Intellectual Property
- Life Sciences
- Materials
- Tech Scout
- Unparalleled Data Quality
- Higher Quality Content
- 60% Fewer Hallucinations
Browse by: Latest US Patents, China's latest patents, Technical Efficacy Thesaurus, Application Domain, Technology Topic, Popular Technical Reports.
© 2025 PatSnap. All rights reserved.Legal|Privacy policy|Modern Slavery Act Transparency Statement|Sitemap|About US| Contact US: help@patsnap.com