Environment-protecting high pressure no-baking carbide residue brick and its making process
A manufacturing method, the technology of calcium carbide slag, applied in the field of building bricks, can solve the problems of high cost of collecting and transporting raw materials, high final cost, complicated process, etc., and achieve the effect of low cost, long service life and simple production process
- Summary
- Abstract
- Description
- Claims
- Application Information
AI Technical Summary
Problems solved by technology
Method used
Examples
Embodiment Construction
[0023] 1. Preparation of liquid phase adhesive
[0024] Take 2 parts of quartz, 3 parts of feldspar, and 1.5 parts of clay by weight and mix them in a crucible, eutectically boil to liquid phase, then naturally cool to room temperature, then add 2 parts of vegetable oil and 0.5 parts of furfural resin, stir and mix evenly, and set aside.
[0025] 2. Making calcium carbide slag bricks
[0026] According to the following table two ingredients:
[0027] ingredients
sandstone
Carbide slag
solid phase adhesive
liquid adhesive
water
Example 1
100 copies
25 copies
12 copies
0.25 parts
3.2 parts
Example 2
100 copies
45 copies
25 copies
0.38 parts
4.5 servings
Example 3
100 copies
38 copies
18 copies
0.40 servings
5.3 parts
Example 4
100 copies
42 copies
16 copies
0.52 parts
7.2 parts
Example 5
100 copies
48 copies
22 copies
0....
PUM
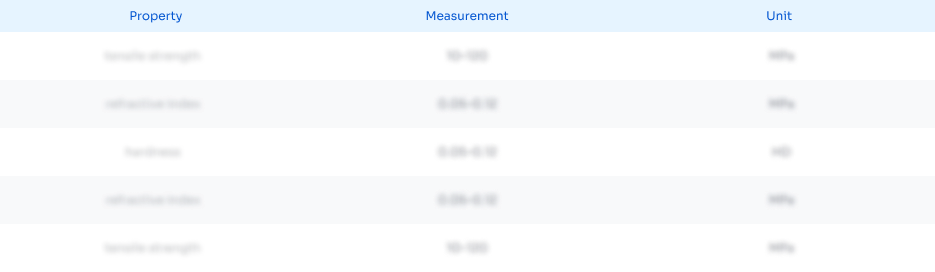
Abstract
Description
Claims
Application Information

- R&D
- Intellectual Property
- Life Sciences
- Materials
- Tech Scout
- Unparalleled Data Quality
- Higher Quality Content
- 60% Fewer Hallucinations
Browse by: Latest US Patents, China's latest patents, Technical Efficacy Thesaurus, Application Domain, Technology Topic, Popular Technical Reports.
© 2025 PatSnap. All rights reserved.Legal|Privacy policy|Modern Slavery Act Transparency Statement|Sitemap|About US| Contact US: help@patsnap.com