Method of extracting high purity acenaphthene from coat tar scrubbing oil
A coal tar, high-purity technology, applied in distillation purification/separation, organic chemistry, etc., can solve the problems of high acenaphthene content, long process, environmental pollution, etc., achieve high recovery rate, simple preparation process, and convenient operation Effect
- Summary
- Abstract
- Description
- Claims
- Application Information
AI Technical Summary
Problems solved by technology
Method used
Examples
Embodiment 1
[0009] The vacuum rectification device is a rectification tower φ30×1600mm, stainless steel triangular packing, 53 trays, and a 500ml three-necked flask for the distillation kettle. Add 400g of coal tar washing oil (acenaphthene content 10.32%) into the three-necked flask, and vacuumize When the pressure is 0.053MPa, start heating to reflux. After 1-2 hours of stabilization, start to extract the distillate. The reflux ratio is 15. When the distillate temperature reaches 235°C, start to collect the acenaphthene fraction. When the temperature reaches 245°C, stop extracting 52.0 g of yellow acenaphthene crystals were obtained, the acenaphthene content was 68.75%, and the acenaphthene yield was 86.60% (based on the acenaphthene in the raw material washing oil).
[0010] Take 10 g of the crystalline acenaphthene fraction, add it to 15 ml of absolute ethanol, heat until the crystals dissolve, then slowly cool to 30° C., the crystals precipitate, filter, wash the crystals with 5 ml of...
Embodiment 2
[0012] With other conditions unchanged, 10ml of ethyl acetate was taken, and after recrystallization, the crystals were washed with 5ml of ethyl acetate and dried to obtain 5.8g of acenaphthene product with acenaphthene content of 99.03%, and the acenaphthene yield was 83.55%.
[0013] It can be seen from the above examples that the advantages of using this method to extract acenaphthene are low energy consumption, simple process, high recovery rate of acenaphthene fraction, high product content, no environmental pollution, and reduced production costs.
PUM
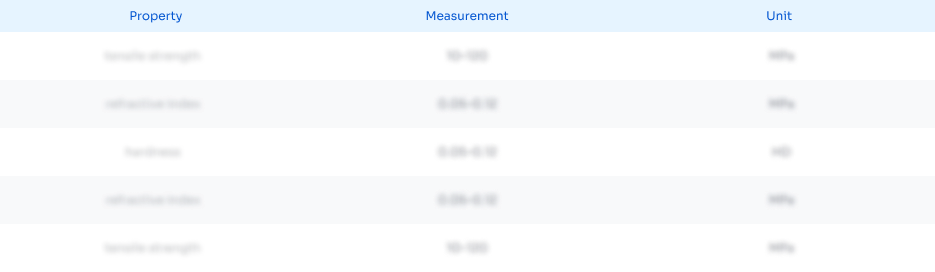
Abstract
Description
Claims
Application Information

- R&D
- Intellectual Property
- Life Sciences
- Materials
- Tech Scout
- Unparalleled Data Quality
- Higher Quality Content
- 60% Fewer Hallucinations
Browse by: Latest US Patents, China's latest patents, Technical Efficacy Thesaurus, Application Domain, Technology Topic, Popular Technical Reports.
© 2025 PatSnap. All rights reserved.Legal|Privacy policy|Modern Slavery Act Transparency Statement|Sitemap|About US| Contact US: help@patsnap.com