Casting material for building material
A technology of building materials and casting materials, applied in the field of building materials, can solve the problems of unfavorable light-weight wall panels on-site construction, insufficient stability of performance, excessive self-weight, etc., and achieve the effects of high mechanical strength, wood saving, and wide application
- Summary
- Abstract
- Description
- Claims
- Application Information
AI Technical Summary
Problems solved by technology
Method used
Image
Examples
Embodiment 1
[0016] Taking the production of light internal partition wall panels as an example to illustrate the formation and use of casting materials:
[0017] (1) Casting material components: (weight percent)
[0018] Proportion at room temperature (about 5-15°C): 35% magnesium oxide, 39.5% magnesium chloride aqueous solution with a percentage concentration of 50-56%, 4.5% chemical mother liquor, which includes: 1.6% urea-formaldehyde resin, ammonium chloride 0.8%, polyvinyl alcohol liquid 1.2%, soda ash 0.6%, bleaching powder 0.3%, 60~80 mesh and sunflower straw powder with water content less than 10% account for 21%.
[0019] (2) Casting material production process:
[0020] a. Prepare the magnesium chloride aqueous solution and the chemical mother liquor respectively according to the above ratio, wherein the magnesium chloride aqueous solution is stirred and left to stand for 24 hours, usually stirred once in about 3 hours.
[0021] b. According to the above ratio, mix sunflower s...
Embodiment 2
[0026] Taking the production of peripheral wall panels as an example to illustrate the formation and use of casting materials:
[0027] Casting material composition: (weight percent)
[0028] Proportion at around 0-10°C: 38% of magnesium oxide, 38.9% of magnesium chloride aqueous solution with a percentage concentration of 50-56%, 5.1% of chemical mother liquor, including: 1.8% of urea-formaldehyde resin, 0.9% of ammonium chloride, 1.3% of polyvinyl alcohol liquid, 1.1% of soda ash, 0.5% of bleaching powder, and 18% of wheat straw powder with 60-80 mesh and water content less than 10%.
[0029] The manufacturing process of the casting material and the manufacturing method of the outer clapboard are the same as in Embodiment 1.
Embodiment 3
[0031] Taking the production of peripheral wall panels as an example to illustrate the formation and use of casting materials
[0032] Casting material composition: (weight percent)
[0033] Proportion at 20-30°C: 32% of magnesium oxide, 32.6% of magnesium chloride aqueous solution with a percentage concentration of 50-56%, 3.4% of chemical mother liquor, including: 1.3% of urea-formaldehyde resin, 0.6% of ammonium chloride %, polyvinyl alcohol liquid 1.0%, soda ash 0.3%, bleaching powder 0.2%, red pine wood sawdust with 60-80 mesh and water content less than 10% accounted for 32%.
[0034] The manufacturing process of the casting material and the manufacturing method of the outer clapboard are the same as in Embodiment 1.
PUM
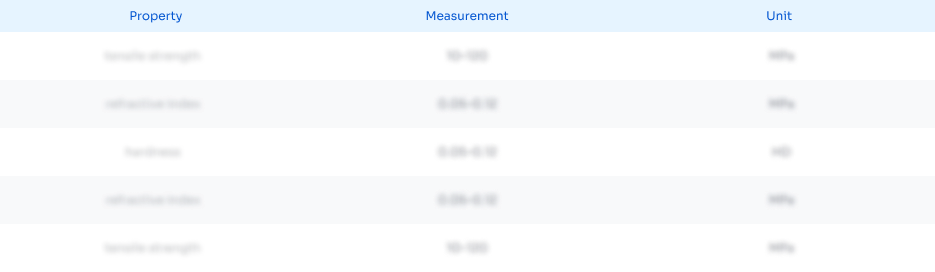
Abstract
Description
Claims
Application Information

- R&D Engineer
- R&D Manager
- IP Professional
- Industry Leading Data Capabilities
- Powerful AI technology
- Patent DNA Extraction
Browse by: Latest US Patents, China's latest patents, Technical Efficacy Thesaurus, Application Domain, Technology Topic, Popular Technical Reports.
© 2024 PatSnap. All rights reserved.Legal|Privacy policy|Modern Slavery Act Transparency Statement|Sitemap|About US| Contact US: help@patsnap.com