Water-white hydrogenating rosin production
A technology of hydrogenated rosin and manufacturing method, which is applied in the direction of natural resin refining, etc., which can solve the problems of high temperature required for the production of water-white hydrogenated rosin, and achieve the effects of reduced economic costs, simple operation of the production process, and reduced requirements for equipment
- Summary
- Abstract
- Description
- Claims
- Application Information
AI Technical Summary
Problems solved by technology
Method used
Examples
Embodiment 1
[0026]The purchased fresh turpentine is crushed and sent to the turpentine tank, and then rinsed and maintained by adding sterilized and low-dissolved oxygen water. The water quality should be 20-30cm higher than the resin surface, and the rinsing water should be replaced every 5-30 days for three consecutive times. Finally, the rosin that has been rinsed is sent to the dissolving tank and added with turpentine to adjust to a concentration of 50-60% by weight of rosin. After heating, dissolving, filtering and clarifying processes, the purified rosin liquid is obtained, and then added to the high pressure tank after metering. In the autoclave, add a skeleton nickel catalyst according to 1-8% of the weight of the feed, after vacuuming and replacing the air in the autoclave with hydrogen, adjust the hydrogen pressure in the autoclave to 8.0-12.0MPa, and start the autoclave stirrer and heating system , raise the temperature to 170-200 ° C, and continuously feed hydrogen, maintain t...
Embodiment 2
[0028] The purchased fresh turpentine is crushed and sent to the turpentine tank, and then rinsed and maintained by adding sterilized and low-dissolved oxygen water. The water quality should be 20-30cm higher than the resin surface, and the rinsing water should be replaced every 5-30 days for three consecutive times. Finally, the rosin that has been rinsed is sent to the dissolving tank and added with turpentine to adjust to a concentration of 50-60% by weight of rosin. After heating, dissolving, filtering and clarifying processes, the purified rosin liquid is obtained, and then added to the high pressure tank after metering. In the autoclave, add a skeleton nickel catalyst according to 7-15% of the weight of the feed, after vacuuming and replacing the air in the autoclave with hydrogen, adjust the hydrogen pressure in the autoclave to 12.0-15.0MPa, and start the autoclave stirrer and heating system , raise the temperature to 140-200°C, and continuously feed hydrogen, maintain ...
Embodiment 3
[0030] Send the rinsed rosin to the dissolving tank and add turpentine to adjust to a concentration of 20-50% by weight of rosin. The hydrogen pressure of the hydrogenation reaction is 4.0-12.0MPa, the reaction temperature is 140-180°C, and the reaction time is 0.5-50%. 3.0 hour, all the other are with embodiment one.
PUM
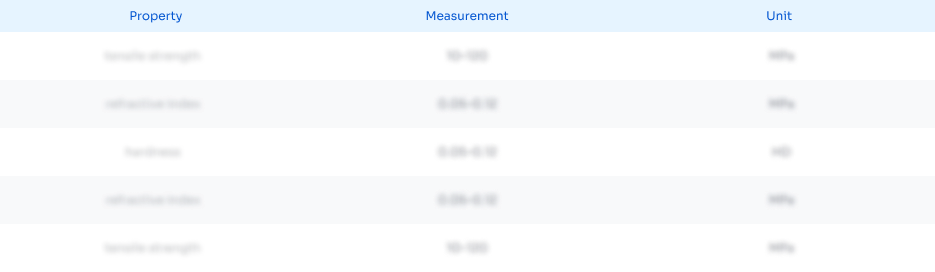
Abstract
Description
Claims
Application Information

- R&D Engineer
- R&D Manager
- IP Professional
- Industry Leading Data Capabilities
- Powerful AI technology
- Patent DNA Extraction
Browse by: Latest US Patents, China's latest patents, Technical Efficacy Thesaurus, Application Domain, Technology Topic, Popular Technical Reports.
© 2024 PatSnap. All rights reserved.Legal|Privacy policy|Modern Slavery Act Transparency Statement|Sitemap|About US| Contact US: help@patsnap.com