Catalyst for production of ethyl benzene using ethylene and benzene and its preparation method and application
A catalyst and ethylene technology, applied in catalyst activation/preparation, molecular sieve catalysts, physical/chemical process catalysts, etc., can solve problems such as increasing production equipment investment
- Summary
- Abstract
- Description
- Claims
- Application Information
AI Technical Summary
Problems solved by technology
Method used
Examples
Embodiment 1
[0034] Embodiment 1: get SiO 2 / Al 2 o 3 30 MCM-22 molecular sieve and Al 2 o 3 The powder is kneaded and extruded according to the weight ratio of 70:30, dried at 120°C and then roasted at 540°C for 5 hours; the obtained strips are exchanged twice with ammonium salt solution at 80-90°C, and then washed with deionized water To neutral, dry at 120°C; vacuum impregnate the dried product with 0.6% HF solution; after impregnation, the strips are dried at 120°C and roasted at 470°C for 2 hours, then treated with saturated water vapor at 310°C After 2 hours, the finished catalyst A was obtained. The F content in the catalyst is 0.98%, Na 2 The O content is 0.02%, and the total acid content per gram of catalyst is (acid centers corresponding to ammonia desorption at 150-600°C) 11.5×10 20 Among them, the ratio of medium strong acid center (acid center for ammonia desorption at 330-600°C) and weak acid center (acid center for ammonia desorption at 150-330°C) is 55:45.
Embodiment 2
[0035] Embodiment 2: take SiO 2 / Al 2 o 3 23 MCM-22 molecular sieve and clay powder are kneaded and extruded according to the weight ratio of 50:50, dried at 120°C and then roasted at 540°C for 4 hours; exchange the obtained strips with ammonium salt solution at 80-90°C 4 times, then washed with deionized water until neutral, dried at 120°C; vacuum impregnated the aforementioned dried product with 0.5% HCl solution; dried at 120°C after impregnation, and then roasted at 470°C for 2 hours , treated with saturated water vapor at 310°C for 2 hours to obtain the finished catalyst B. The content of Cl in the catalyst is 0.3%, Na 2 The O content is 0.01%, and the total acid content per gram of catalyst is (acid centers corresponding to ammonia desorption at 150-600°C) 9.5×10 20 One, wherein the ratio of medium-strong acid center (acid center for ammonia desorption at 330-600°C) and weak acid center (acid center for ammonia desorption at 150-330°C) is 50:50.
Embodiment 3
[0036] Embodiment 3: get SiO 2 / Al 2 o 3 39 MCM-22 molecular sieve and Al 2 o 3 The powder is kneaded and extruded according to the weight ratio of 80:20, dried at 120°C and then roasted at 540°C for 3 hours; the obtained strips are exchanged twice with ammonium salt solution at 80-90°C, and then washed with deionized water To neutral, after drying at 120°C, vacuum impregnate the dried product with 0.8% HF solution; after impregnation, the strips are dried at 120°C and roasted at 470°C for 2 hours, then heated at 320°C with saturated water vapor After 2 hours of treatment, the finished catalyst C was obtained. The F content in the catalyst is 1.2%, Na 2 The O content is 0.01%, and the total acid content per gram of catalyst is (acid centers corresponding to ammonia desorption at 150-600°C) 14.2×10 20 One, wherein the ratio of medium-strong acid center (acid center for ammonia desorption at 330-600°C) and weak acid center (acid center for ammonia desorption at 150-330°C) ...
PUM
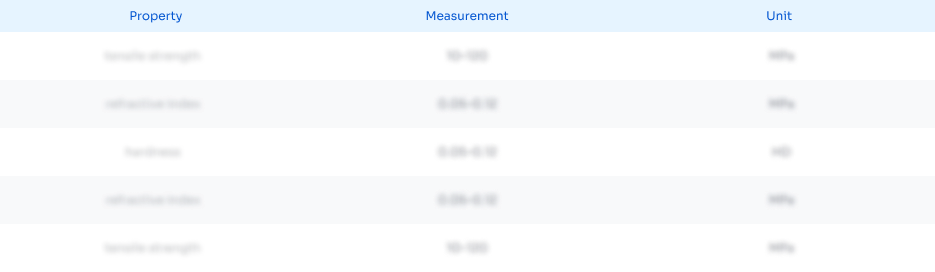
Abstract
Description
Claims
Application Information

- R&D
- Intellectual Property
- Life Sciences
- Materials
- Tech Scout
- Unparalleled Data Quality
- Higher Quality Content
- 60% Fewer Hallucinations
Browse by: Latest US Patents, China's latest patents, Technical Efficacy Thesaurus, Application Domain, Technology Topic, Popular Technical Reports.
© 2025 PatSnap. All rights reserved.Legal|Privacy policy|Modern Slavery Act Transparency Statement|Sitemap|About US| Contact US: help@patsnap.com