Process for preparing nano porous graphite
A nano-porous and graphite technology, applied in the field of nano-materials, can solve the problem of large pores of expanded graphite and achieve the effect of improving the adsorption capacity
- Summary
- Abstract
- Description
- Claims
- Application Information
AI Technical Summary
Problems solved by technology
Method used
Image
Examples
Embodiment 1
[0019] Take 3 grams of flake graphite with a fineness of 80 mesh and a carbon content of 90%, 30 grams of sulfuric acid with a concentration of 98% and 2 grams of potassium permanganate, put them into a beaker, stir and mix with a glass rod. Then put the beaker into a constant temperature water bath, and the temperature of the water bath is set at 45°C. The mixture was continuously stirred with a magnetic rod, and the stirring RPM was set at 300. After the intercalation, the water washing procedure was carried out. Filter the mixture with a 200-mesh stainless steel mesh, then put the filter residue into a 500ml beaker, enter 400ml of clear water, stir thoroughly with a glass rod, and then filter with a 200-mesh stainless steel mesh. Repeat wash twice. Measure the pH of the last stirred solution to be 0.2. The final filtered residue was placed in a glass petri dish and dried in an oven. The temperature of the oven is 60° C., and the duration of the drying process is 10 hour...
Embodiment 2
[0021] Take 3 grams of flake graphite with a fineness of 50 mesh and a carbon content of 95%, 30 grams of sulfuric acid with a concentration of 98% and 2 grams of potassium permanganate, put them into a beaker, stir and mix them with a glass rod. Then put the beaker into a constant temperature water bath, and the temperature of the water bath is set to 50°C. The mixture was continuously stirred with a magnetic rod, and the stirring RPM was set at 300. After the intercalation, the water washing procedure was carried out. Filter the mixture with a 200-mesh stainless steel mesh, then put the filter residue into a 500ml beaker, enter 400ml of clear water, stir thoroughly with a glass rod, and then filter with a 200-mesh stainless steel mesh. Repeat wash 4 times. Measure the pH of the last stirred solution to be 3.0. The final filtered residue was placed in a glass petri dish and dried in an oven. The temperature of the oven is 60° C., and the duration of the drying process is ...
Embodiment 3
[0023] Take 3 grams of flake graphite with a fineness of 80 mesh and a carbon content of 90%, 30 grams of sulfuric acid with a concentration of 98% and 2 grams of potassium permanganate, put them into a beaker, stir and mix with a glass rod. Then put the beaker into a constant temperature water bath, and the temperature of the water bath is set to 60°C. The mixture was continuously stirred with a magnetic rod, and the stirring RPM was set at 300. After the intercalation, the water washing procedure was carried out. Filter the mixture with a 200-mesh stainless steel mesh, then put the filter residue into a 500ml beaker, enter 400ml of clear water, stir thoroughly with a glass rod, and then filter with a 200-mesh stainless steel mesh. Repeat washing 6 times. The pH of the last stirred solution was measured to be 6.0. The final filtered residue was placed in a glass petri dish and dried in an oven. The temperature of the oven is 60° C., and the duration of the drying process ...
PUM
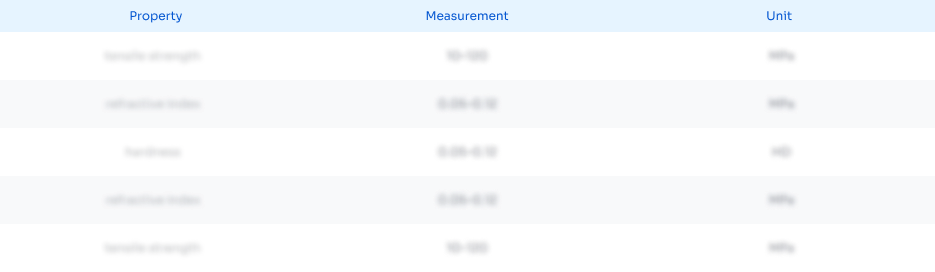
Abstract
Description
Claims
Application Information

- Generate Ideas
- Intellectual Property
- Life Sciences
- Materials
- Tech Scout
- Unparalleled Data Quality
- Higher Quality Content
- 60% Fewer Hallucinations
Browse by: Latest US Patents, China's latest patents, Technical Efficacy Thesaurus, Application Domain, Technology Topic, Popular Technical Reports.
© 2025 PatSnap. All rights reserved.Legal|Privacy policy|Modern Slavery Act Transparency Statement|Sitemap|About US| Contact US: help@patsnap.com