Method for forming antifouling coating and antifouling material having antifouling coating
An antifouling and coating technology, applied in antifouling/underwater coatings, devices for coating liquids on the surface, coatings, etc., can solve the problems of insufficient photocatalysts to prevent pollution, high cost, and inability to obtain adhesion Power and other issues
- Summary
- Abstract
- Description
- Claims
- Application Information
AI Technical Summary
Problems solved by technology
Method used
Image
Examples
Embodiment 1
[0063] (1) Production of substrate
[0064] The base material was prepared by coating an acrylic resin paint (acrylic cleanser, manufactured by Nippon Paint Co., Ltd.) with a thickness of 30 μm on an aluminum plate of 50×100×2 mm, followed by baking treatment at 160°C for 60 minutes.
[0065] (2) Plasma discharge treatment
[0066] Plasma discharge treatment is used such as figure 1 The plasma discharge treatment device shown is performed. After degreasing the acrylic resin surface (treatment surface) of the above substrate with ethanol, the substrate is placed in a 10×10×30 cm glass processing chamber, the processing chamber is evacuated, and then O 2 The gas is formed into 1torr, and a voltage with an output power of 100W is applied for 10 minutes to perform plasma discharge treatment.
[0067] (3) Measurement of contact angle
[0068] Use a contact angle meter to measure the water contact angle within 30 minutes. The measurement results are shown in Table 2. The contact angle ...
Embodiment 2
[0076] In addition to the atmosphere gas during plasma discharge treatment, from O 2 Change the gas to N 2 Except for the gas, the experiment was performed in the same manner as in Example 1.
Embodiment 3
[0078] In addition to the atmosphere gas during plasma discharge treatment, from O 2 The experiment was performed in the same manner as in Example 1, except that the gas was changed to Ar gas.
PUM
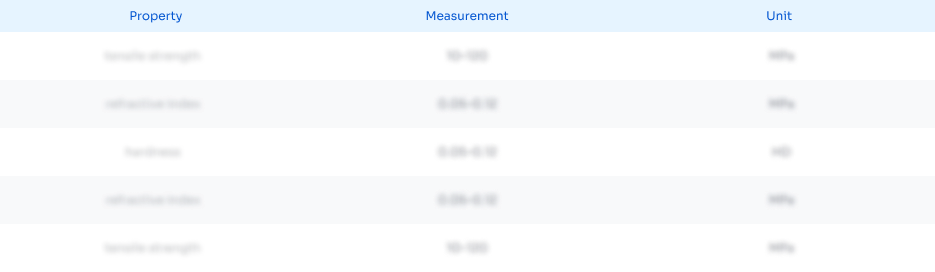
Abstract
Description
Claims
Application Information

- Generate Ideas
- Intellectual Property
- Life Sciences
- Materials
- Tech Scout
- Unparalleled Data Quality
- Higher Quality Content
- 60% Fewer Hallucinations
Browse by: Latest US Patents, China's latest patents, Technical Efficacy Thesaurus, Application Domain, Technology Topic, Popular Technical Reports.
© 2025 PatSnap. All rights reserved.Legal|Privacy policy|Modern Slavery Act Transparency Statement|Sitemap|About US| Contact US: help@patsnap.com