Load catalyst containing nickel and iron and its application
A technology for supporting catalysts and catalysts, which is applied to catalyst carriers, physical/chemical process catalysts, chemical instruments and methods, etc., can solve the problems of difficult separation and low catalyst residues, achieve simple regeneration treatment, good industrialization prospects, and avoid separation. difficult effect
- Summary
- Abstract
- Description
- Claims
- Application Information
AI Technical Summary
Problems solved by technology
Method used
Examples
Embodiment 1
[0023] (1) Preparing the complex supported carrier of the catalyst. Use cross-linked polyacrylic acid ion exchange resin as the carrier of catalyst iron halide, wash with 5% lye, change the ion exchange resin from hydrogen form to sodium form, then wash with deionized water to pH = 9, and vacuum dry at 80°C Afterwards, pulverized by a ball mill, and then vacuum-dried to obtain a cross-linked polyacrylic acid ion exchange resin powder PAA(Na).
[0024] (2) Preparation of supported passivator. Take 1 part of ferric trichloride FeCl 3 After dissolving in 10 parts of methanol, add 3 parts of cross-linked polyacrylic acid ion exchange resin powder, stir and reflux at 70°C for 3 hours, remove methanol and vacuum dry to obtain PAA-FeCl 3 Crude. The crude product was eluted with methanol until it was colorless, and after vacuum drying, PAA-FeCl 3 .
[0025] (3) Preparation of loaded activator. Take 1 part NiCl 2 After being placed in 10 parts of methanol and fully stirred, add ...
Embodiment 2
[0029] (1) Preparing the complex supported carrier of the catalyst. Use cross-linked polyacrylic acid ion exchange resin as the carrier of catalyst iron halide, wash with 3% lye, change the ion exchange resin from hydrogen form to sodium form, then wash with deionized water to pH = 9, and vacuum dry at 80°C Afterwards, pulverized by a ball mill, and then vacuum-dried to obtain a cross-linked polyacrylic acid ion exchange resin powder PAA(Na).
[0030] (2) Preparation of supported passivator. Take 1 part of iron tribromide FeBr 3 After dissolving in 10 parts of methanol, add 3 parts of cross-linked polyacrylic acid ion exchange resin powder, stir and reflux at 70°C for 3 hours, remove methanol and vacuum dry to obtain PAA-FeBr 3 Crude. The crude product was eluted with methanol until it was colorless, and after vacuum drying, PAA-FeBr 3 .
[0031] (3) Preparation of loaded activator. Take 1 part NiBr 2 After being placed in 10 parts of methanol and fully stirred, add 30 ...
Embodiment 3
[0035] (1) Preparing the complex supported carrier of the catalyst. Use cross-linked polyacrylic acid ion exchange resin as the carrier of catalyst iron halide, wash with 4% lye, change the ion exchange resin from hydrogen form to sodium form, then wash with deionized water to pH = 9, and vacuum dry at 80°C Afterwards, pulverized by a ball mill, and then vacuum-dried to obtain a cross-linked polyacrylic acid ion exchange resin powder PAA(Na).
[0036] (2) Preparation of supported passivator. Take 1 part of iron tribromide FeBr 3 After dissolving in 10 parts of methanol, add 3 parts of cross-linked polyacrylic acid ion exchange resin powder, stir and reflux at 70°C for 3 hours, remove methanol and vacuum dry to obtain PAA-FeBr 3 Crude. The crude product was eluted with methanol until it was colorless, and after vacuum drying, PAA-FeBr 3 .
[0037] (3) Preparation of loaded activator. Take 1 part NiCl 2 After being placed in 10 parts of methanol and fully stirred, add 30 ...
PUM
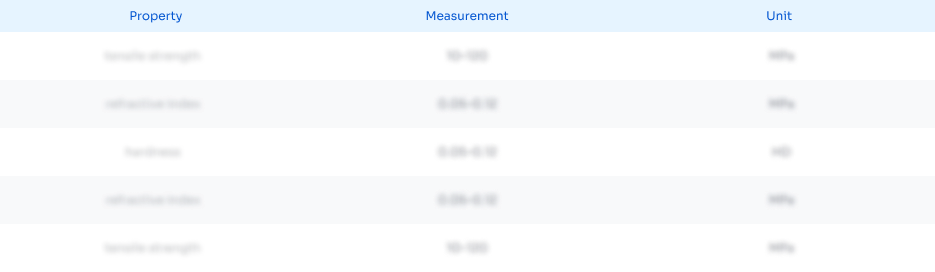
Abstract
Description
Claims
Application Information

- R&D
- Intellectual Property
- Life Sciences
- Materials
- Tech Scout
- Unparalleled Data Quality
- Higher Quality Content
- 60% Fewer Hallucinations
Browse by: Latest US Patents, China's latest patents, Technical Efficacy Thesaurus, Application Domain, Technology Topic, Popular Technical Reports.
© 2025 PatSnap. All rights reserved.Legal|Privacy policy|Modern Slavery Act Transparency Statement|Sitemap|About US| Contact US: help@patsnap.com