Method for producing rubber drum
A technology of rubber roller and manufacturing method, which is applied in the direction of manufacturing tools, machine tools designed for grinding the rotating surface of workpieces, grinding machines, etc., which can solve the problems of large shaft core load, poor grinding accuracy, and damage to shape accuracy, so as to improve production Efficiency, excellent grinding accuracy, and shortened grinding time
- Summary
- Abstract
- Description
- Claims
- Application Information
AI Technical Summary
Problems solved by technology
Method used
Image
Examples
Embodiment
[0055] According to the grinding step S of the present invention, on the basis of the following conditions, the rubber cylinder with length L (240mm) and diameter D (18mm) is rotated at a rotational speed of 150rpm, and is ground with a grinding tool at the same time, and the measurement process becomes the surface Grinding time for products with a diameter of (15) mm.
[0056] Abrasives
[0057] ·Width: 260mm
[0058] ·Fineness: 80 mesh
[0059] ·Rotation speed: 2000rpm
[0060] Grinding step (no vibration)
[0061] · Preparatory grinding steps
[0062] Forward speed V1: 21mm / min
[0063] Grinding time T1: 3 seconds
[0064] ·Intermediate grinding step
[0065] Forward speed V2: 17mm / min
[0066] Grinding time T2: 3 seconds
[0067] ·Finish grinding step
[0068] Forward speed V3: 1mm / min
[0069] Grinding time T3: 12 seconds
[0070] · Non-spark grinding steps
[0071] Forward speed V4: 0mm / min
[0072] Grinding time T4: 5 seconds
[0073] In contrast, on the ...
PUM
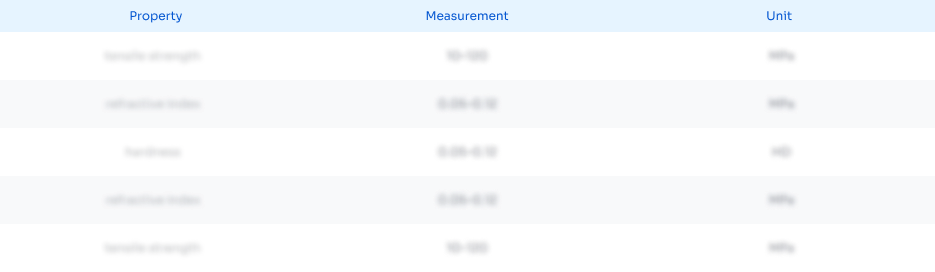
Abstract
Description
Claims
Application Information

- Generate Ideas
- Intellectual Property
- Life Sciences
- Materials
- Tech Scout
- Unparalleled Data Quality
- Higher Quality Content
- 60% Fewer Hallucinations
Browse by: Latest US Patents, China's latest patents, Technical Efficacy Thesaurus, Application Domain, Technology Topic, Popular Technical Reports.
© 2025 PatSnap. All rights reserved.Legal|Privacy policy|Modern Slavery Act Transparency Statement|Sitemap|About US| Contact US: help@patsnap.com