Heat treatment method for improving high-niobium reinforcing type monocrystal high temp alloy use property
A heat treatment method and superalloy technology, applied in chemical instruments and methods, post-treatment, single crystal growth, etc., can solve the problem that the strength potential of cast IN718 alloy cannot be fully realized, and achieve the purpose of expanding the scope of use, improving plasticity and improving strength. Effect
- Summary
- Abstract
- Description
- Claims
- Application Information
AI Technical Summary
Problems solved by technology
Method used
Examples
Embodiment 1
[0014] Example 1 Treatment of Single Crystal IN718 Alloy
[0015] A homogenization and aging heat treatment system of the present invention for high-niobium-strengthened superalloys is as follows: take the single-crystal cast IN718 alloy as sample 1, heat it at 1160°C for 20 hours, eliminate the harmful phase Laves phase and niobium segregation, and the alloy The melting point rose to 1240°C. Then heat the alloy to 1240°C, keep it warm for 20 hours, and air-cool (homogenization treatment); keep it at 720°C for 8 hours, cool it to 620°C at a cooling rate of 50°C per hour, keep it at 620°C for 8 hours, and air-cool (aging treatment).
[0016] Take another sample of the same material and size using a conventional heat treatment system (J.T.Guo, L.Z.Zhou, The effect of phosphorus, sulfur and silicon, on segregation, solidification and mechanical properties in cast alloy 718.in'Superalloys 1996', eds.By R.D.kissinger et al., TMS, 1996, p.451) treatment: heat preservation at 1090°C...
Embodiment 2
[0021] Embodiment 2 is to the processing of IN718 alloy
[0022] The single-crystal cast IN718 alloy was taken as specimen 2, which was subjected to high-temperature homogenization treatment, that is, heat preservation at 1145°C for 25 hours, to eliminate the harmful phase Laves phase and niobium segregation, and the melting point of the alloy rose to 1240°C. Then heat the alloy to 1200°C, keep it warm for 30 hours, and cool it in air; then carry out conventional aging treatment to precipitate the strengthening phase, that is, keep it at 720°C for 8 hours, cool it to 620°C at an average speed of 50°C per hour, and keep it at 620°C for 8 hours. air cooled.
[0023] The cast polycrystalline IN718 alloy was treated by hot isostatic pressing heat treatment in the prior art: after hot isostatic pressing: 1121° C., 102.9 MPa pressure, heat preservation for 3 hours. Then keep it at 1065°C for 1 hour, keep it at 718°C for 8 hours, cool it to 621°C at an average speed of 50°C per hour...
Embodiment 3
[0026] Embodiment 3 to the treatment of K718 alloy
[0027] Select (single crystal) K718 alloy as specimen 3, the difference from Example 1 is that the homogenization treatment is a stage:
[0028] 1. High temperature homogenization treatment:
[0029] Place the sample in a temperature environment of 1170 ° C to eliminate harmful phases and increase the melting point of the alloy, and keep it warm for 50 hours until the Laves phase of the test piece is dissolved and Nb segregation is eliminated;
[0030] 2. Conventional aging treatment precipitation strengthening phase:
[0031] The aging treatment adopts the standard aging treatment system of high-niobium strengthened alloys: heat preservation at 720°C for 8 hours, cooling in a uniform furnace to 620°C for 2 hours, heat preservation at 620°C for 8 hours, and air cooling.
[0032]In addition, the conventional heat treatment of polycrystalline casting is adopted (Zhao Jingchen, Wang Bin, Sun Jiahua, Effect of homogenization t...
PUM
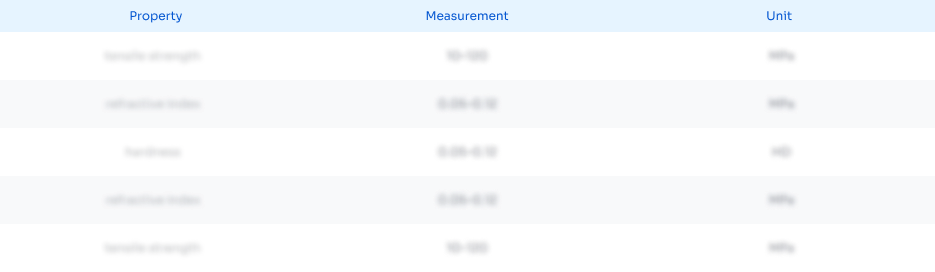
Abstract
Description
Claims
Application Information

- R&D
- Intellectual Property
- Life Sciences
- Materials
- Tech Scout
- Unparalleled Data Quality
- Higher Quality Content
- 60% Fewer Hallucinations
Browse by: Latest US Patents, China's latest patents, Technical Efficacy Thesaurus, Application Domain, Technology Topic, Popular Technical Reports.
© 2025 PatSnap. All rights reserved.Legal|Privacy policy|Modern Slavery Act Transparency Statement|Sitemap|About US| Contact US: help@patsnap.com