Plate shape and thickness-controlling rolling method and corresponding gap-less roller mill
A control plate, no gap technology, applied in the direction of metal rolling, contour control, metal rolling, etc., can solve the problems of easy vibration, affecting the accuracy of plate shape and plate thickness control, etc.
- Summary
- Abstract
- Description
- Claims
- Application Information
AI Technical Summary
Problems solved by technology
Method used
Image
Examples
Embodiment Construction
[0022] The technical scheme of the present invention is described in detail below in conjunction with accompanying drawing and specific embodiment:
[0023] The method for adjusting the shape and thickness of the plate in the present invention is to control the thickness and shape of the plate by moving and crossing the work rolls. Symmetrically intersect at 1 / 2 of the width of the rolled steel plate, and the two work rolls move horizontally and laterally to the same side at the intersection point, and work at the positions of both ends of the rolled steel plate, the axis of one end of the upper work roll and the lower work roll The axes of the other ends of the rollers respectively intersect the axes of the backup rollers. The intersection angle α of the upper and lower work rolls is greater than 0 degrees and less than or equal to 1.5 degrees; the offset of the upper and lower work rolls at the intersection is greater than 0 and less than or equal to 15 mm.
[0024] see F...
PUM
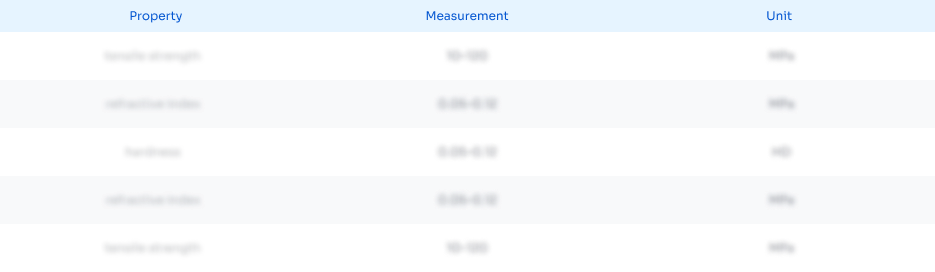
Abstract
Description
Claims
Application Information

- R&D
- Intellectual Property
- Life Sciences
- Materials
- Tech Scout
- Unparalleled Data Quality
- Higher Quality Content
- 60% Fewer Hallucinations
Browse by: Latest US Patents, China's latest patents, Technical Efficacy Thesaurus, Application Domain, Technology Topic, Popular Technical Reports.
© 2025 PatSnap. All rights reserved.Legal|Privacy policy|Modern Slavery Act Transparency Statement|Sitemap|About US| Contact US: help@patsnap.com