Roasting method for producing sodium chromate using chrome iron ore as raw material
A technology of chromite and sodium chromate, applied in the direction of chromate/dichromate, etc., can solve the problems of difficult filtration and washing, serious slag belt damage, environmental pollution, etc., and achieve clinker performance and filtration and washing performance Improve, prevent material scarring, improve the effect of utilization
- Summary
- Abstract
- Description
- Claims
- Application Information
AI Technical Summary
Problems solved by technology
Method used
Examples
example 1
[0027] Weigh and crush the 200 mesh sieve containing Cr 2 o 3 Add 10g of 53.6% chromite, add 15g of sodium carbonate, 18g of magnesite, and mix well. Roasting at 1150°C for 40 minutes, the clinker is sandy, the transfer rate is 99.65%, and the acid-soluble hexavalent chromium is 0.02%.
example 2
[0029] Weigh and crush the 200 mesh sieve containing Cr 2 o 3 Add 10g of 52.1% chromite, add 8g of sodium carbonate, 20g of magnesite, 10g of returned slag, and mix well. Roasting at 1150°C for 30 minutes, the clinker is sandy, the transfer rate is 99.3%, and the acid-soluble hexavalent chromium is 0.04%.
example 3
[0031] Weigh and crush the 200 mesh sieve containing Cr 2 o 3 Add 10g of 45.3% chromite, add 8g of sodium carbonate, 40g of magnesite, and mix well. Roasting at 1100°C for 60 minutes, the clinker is sandy, the transfer rate is 98.91%, and the acid-soluble hexavalent chromium is 0.048%.
PUM
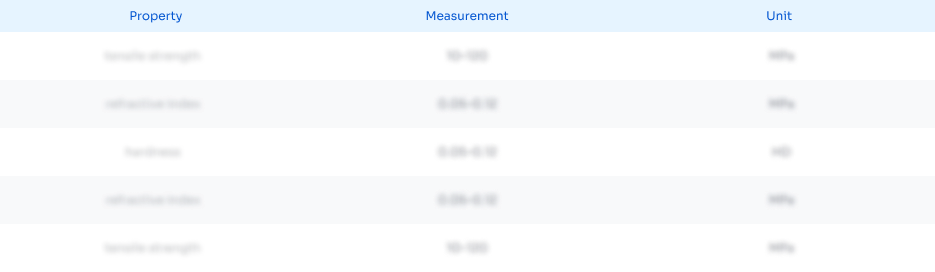
Abstract
Description
Claims
Application Information

- R&D
- Intellectual Property
- Life Sciences
- Materials
- Tech Scout
- Unparalleled Data Quality
- Higher Quality Content
- 60% Fewer Hallucinations
Browse by: Latest US Patents, China's latest patents, Technical Efficacy Thesaurus, Application Domain, Technology Topic, Popular Technical Reports.
© 2025 PatSnap. All rights reserved.Legal|Privacy policy|Modern Slavery Act Transparency Statement|Sitemap|About US| Contact US: help@patsnap.com