Process for prefabricating cold-drawn plate for side wall large plate of passenger train
A technology for cold-drawn prefabricated panels and railway passenger cars, which is applied in railway car bodies, railway car body parts, railway transportation, etc., can solve the problem of difficulty in reaching the leveling level, low flatness of side wall panels, and uneven internal stress of large panels. and other problems to achieve the effect of saving investment, saving production materials and man-hours, and shortening the production cycle
- Summary
- Abstract
- Description
- Claims
- Application Information
AI Technical Summary
Problems solved by technology
Method used
Examples
Embodiment Construction
[0010] Cut the steel plate (06CuPCrNi) into a 25-meter-long large coil. After uncoiling, put one end of the large plate into the mold of the fixing mechanism, and introduce the other end into the mold of the stretching mechanism. position. Adjust the pressure of the fixing mechanism system to 18Mpa and press the large plate tightly to make the large plate rectangular and then maintain the pressure for 1 minute; start the stretching mechanism, stretch the large plate to 200-270mm, stop stretching and hold the pressure for 2 minutes, and stretch the plate The straightness of the straightness is not greater than 2mm within 25m, and the deflection is not greater than 3mm; return the large plate to eliminate the elastic deformation of the large plate (generally around 50mm); loosen the fixing mechanism and the stretching mechanism respectively, so that the large plate is separated from the mold and Move to the side wall welding tire position for welding.
PUM
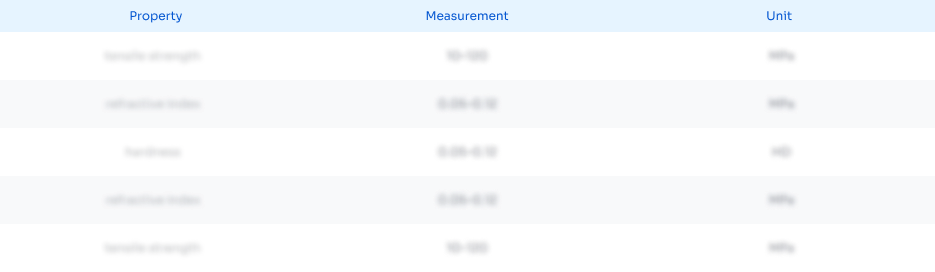
Abstract
Description
Claims
Application Information

- R&D Engineer
- R&D Manager
- IP Professional
- Industry Leading Data Capabilities
- Powerful AI technology
- Patent DNA Extraction
Browse by: Latest US Patents, China's latest patents, Technical Efficacy Thesaurus, Application Domain, Technology Topic, Popular Technical Reports.
© 2024 PatSnap. All rights reserved.Legal|Privacy policy|Modern Slavery Act Transparency Statement|Sitemap|About US| Contact US: help@patsnap.com