High-density CD and its making process
A production method and high-density technology, which are applied in the directions of recording/reproducing by optical methods, manufacturing of optical record carriers, optical record carriers, etc., can solve the problems of large error value, high cost, non-standard ablation pits, etc. The production process is simple, the use is convenient, and the cost is low.
- Summary
- Abstract
- Description
- Claims
- Application Information
AI Technical Summary
Problems solved by technology
Method used
Image
Examples
Embodiment Construction
[0017] Such as Figure 1~2 Shown, a kind of high-density disc manufacturing method is characterized in that a) blow molding standard film base; b) coating photosensitive layer on the surface of the film base; c) exposure and washing by ultraviolet light; d) forming black spots ( signal); e) vacuum aluminized film layer;
[0018] A high-density optical disc is characterized in that a protective layer 3 is provided on a film base 1, and a photosensitive layer 2 is arranged between the film base 1 and the protective layer 3. The present invention adopts the chemical type to directly obtain the black dot signal, and uses the conventional flushing method. At the same time, due to the use of chemical raw materials to form a signal group, a one-time program CD can be derived (that is, after the protective film bag is opened, the signal is oxidized by air components, causing chemical changes to lose the signal). Such as image 3 As shown, when the laser beam hits the convex island ...
PUM
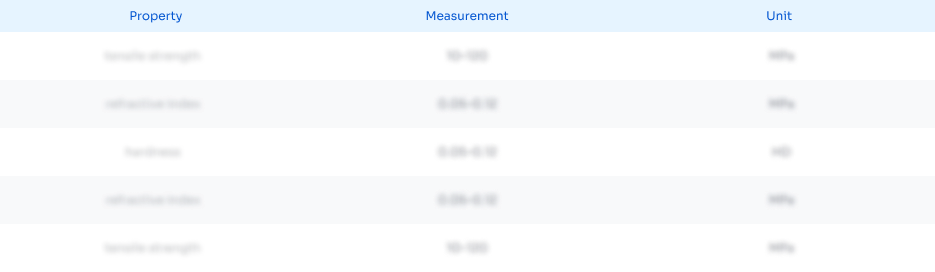
Abstract
Description
Claims
Application Information

- R&D
- Intellectual Property
- Life Sciences
- Materials
- Tech Scout
- Unparalleled Data Quality
- Higher Quality Content
- 60% Fewer Hallucinations
Browse by: Latest US Patents, China's latest patents, Technical Efficacy Thesaurus, Application Domain, Technology Topic, Popular Technical Reports.
© 2025 PatSnap. All rights reserved.Legal|Privacy policy|Modern Slavery Act Transparency Statement|Sitemap|About US| Contact US: help@patsnap.com