Excitation of switch magnetic resistance motor
A reluctance motor and multi-phase switch technology, applied in the direction of AC motor control, electronic commutation motor control, single motor speed/torque control, etc., can solve problems such as not suitable for driving devices
- Summary
- Abstract
- Description
- Claims
- Application Information
AI Technical Summary
Problems solved by technology
Method used
Image
Examples
Embodiment Construction
[0034] The present invention is implemented in a preferred embodiment in a transmission system such as that shown in FIG. 1 with a commutation circuit for each phase shown in FIG. 2 . According to the invention, by programming the controller 14, the control strategy is adapted to develop the idle configuration of the conversion circuit.
[0035] Figure 6 A typical rotor position sensor (rpt) of the three-phase four-pole drive in Fig. 1 is schematically shown in . Three sensors are shown arranged mechanically offset by an angle of 120°, but any offset arrangement equal to an electrical angle of 120° may be used. This schematic has teeth with unit void ratio. In practice, this can be varied slightly to accommodate any non-ideal characteristics of the sensor, such as the beam width of an optical sensor or the fringing flux of a Hall effect sensor, so that the final signal of the rpt is at or acceptably close to a mark-to-space ratio of 1 .
[0036] Figure 6 The output of the...
PUM
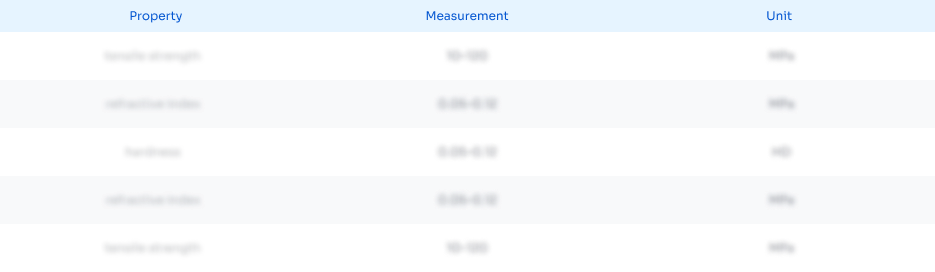
Abstract
Description
Claims
Application Information

- R&D
- Intellectual Property
- Life Sciences
- Materials
- Tech Scout
- Unparalleled Data Quality
- Higher Quality Content
- 60% Fewer Hallucinations
Browse by: Latest US Patents, China's latest patents, Technical Efficacy Thesaurus, Application Domain, Technology Topic, Popular Technical Reports.
© 2025 PatSnap. All rights reserved.Legal|Privacy policy|Modern Slavery Act Transparency Statement|Sitemap|About US| Contact US: help@patsnap.com