Synthesis of fused liquid crystal of chitosan grafted polylactic acid
A synthesis method, chitosan technology, applied in the field of synthesis of chitosan-grafted polylactic acid melt-induced liquid crystals, can solve the problems of application limitations, unclear physiological effects of polyvinyl alcohol, poor hydrophilicity, etc., and achieve excellent biophase Capacitance, excellent biodegradability, effect of improving solubility
- Summary
- Abstract
- Description
- Claims
- Application Information
AI Technical Summary
Problems solved by technology
Method used
Examples
Embodiment 1
[0012] Implementation of chitosan with 50% deacetylation degree and lactide molar ratio of 1:1.
[0013] The chitosan with a deacetylation degree of 50% was dried in a vacuum oven for 48 hours to remove the adsorbed water on its surface. Weigh 0.05 mol of chitosan and add it to the reactor, pour nitrogen into it repeatedly three times, then degas under vacuum for 1 hour, add 40 ml of dried toluene as a dispersant, and prepare it into a 1.25 mol toluene dispersion . Weigh 0.05 mol of triethylaluminum to prepare a 15% toluene solution. Add the triethylaluminum solution dropwise to the chitosan toluene dispersion at room temperature, and react for another 1 hour when no gas is generated. Add 0.05 mol of lactide degassed by vacuum for 1 hour, then place the reactor in an oil bath pre-heated to 70°C, react for more than 20 hours, pour the reaction solution into ethanol to allow it to fully precipitate, and filter and dry After obtaining the product. Because the deacetylation de...
Embodiment 2
[0015] The implementation of chitosan and lactide with a degree of deacetylation of 94% at a ratio of 1:1.
[0016] The chitosan with a deacetylation degree of 94% was dried in a vacuum oven for 48 hours to remove the adsorbed water on its surface. Weigh 0.05mol chitosan and add it into the reactor, flush with nitrogen three times, and then degas under vacuum for 1 hour. Add 60 ml of dried toluene as a dispersant to prepare a 0.83 mole toluene dispersion. Weigh 0.05 mol of triethylaluminum to prepare a 15% toluene solution. Add the triethylaluminum solution dropwise to the chitosan toluene dispersion at room temperature, and react for another 1 hour when no gas is produced. Add 0.05 mol of lactide that has been vacuum degassed for 1 hour, then place the reactor in an oil bath pre-heated to 70°C, and after 20 hours of reaction, pour the reaction solution into ethanol to make it fully precipitate, filter and dry After obtaining the product. In this embodiment, chitosan with ...
Embodiment 3
[0018] Acetyl degree 94% chitosan and lactide 1:60 implementation.
[0019] The chitosan with a deacetylation degree of 94% was dried in a vacuum oven for 48 hours to remove the adsorbed water on its surface. Weigh 0.005 mol of chitosan and add it into the reactor, flush with nitrogen for three times, and then degas under vacuum for 1 hour. Add 100 ml of dried toluene as a dispersant to prepare a 0.05 mol toluene dispersion. Weigh 0.005 mol of triethylaluminum to prepare a 15% toluene solution. Add the triethylaluminum solution dropwise to the chitosan toluene dispersion at room temperature, and react for another 1 hour when no gas is produced. Add 0.3 mol of lactide that has been vacuum degassed for 1 hour, then place the reactor in an oil bath preheated to 70°C, and after 20 hours of reaction, pour the reaction solution into ethanol to make it fully precipitate, filter and dry After obtaining the product. Due to the use of chitosan with a high degree of deacetylation and...
PUM
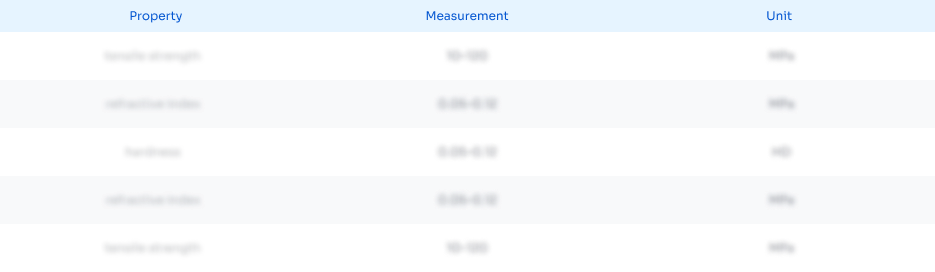
Abstract
Description
Claims
Application Information

- Generate Ideas
- Intellectual Property
- Life Sciences
- Materials
- Tech Scout
- Unparalleled Data Quality
- Higher Quality Content
- 60% Fewer Hallucinations
Browse by: Latest US Patents, China's latest patents, Technical Efficacy Thesaurus, Application Domain, Technology Topic, Popular Technical Reports.
© 2025 PatSnap. All rights reserved.Legal|Privacy policy|Modern Slavery Act Transparency Statement|Sitemap|About US| Contact US: help@patsnap.com