Synthesis of degradable poly-beta-oxybate
A technology of hydroxybutyrate and ethyl hydroxybutyrate, applied in the field of completely degradable plastics, can solve the problems of complex reaction process and low degree of polymer polymerization, and achieve the effects of abundant sources, low cost and large output
- Summary
- Abstract
- Description
- Claims
- Application Information
AI Technical Summary
Problems solved by technology
Method used
Examples
Embodiment 1
[0012] The preparation of embodiment 1 (1) β-hydroxybutyraldehyde
[0013] Reactant acetaldehyde 88g, solvent benzene 88g, catalyst NaOH aqueous solution 26.7g, reaction temperature 4-5°C, reaction time 1.0 hour, use acetic acid to neutralize the catalyst, the product contains acetaldehyde 19.36g, enaldehyde 0.89g, β -Hydroxybutyraldehyde is 61.68g, the reaction yield is: 70.1%, and the conversion rate of acetaldehyde is: 78.0%. (2) Preparation of β-hydroxybutyric acid
[0014] Reactant β-hydroxybutyraldehyde 161g, solvent ethyl acetate 144.7ml, catalyst cobalt acetate 1.5852g, reaction time 5 hours, reaction temperature 90°C, reaction pressure 10MPa, β-hydroxybutyric acid in the product was 165.57g, butene The aldehyde is 14.75g, the reaction yield is: 88.9%, and the conversion rate is: 90.9%. (3) Preparation of ethyl β-hydroxybutyrate
[0015] Reactant β-hydroxybutyric acid 10.41g, ethanol 3.84g, catalyst p-toluenesulfonic acid 1g, reaction time is 3 hours, reaction tempe...
Embodiment 2
[0017] The preparation of embodiment 2 (1) β-hydroxybutyraldehyde
[0018] Reactant acetaldehyde 90g, solvent benzene 54g, catalyst NaOH 50.7g, reaction temperature 4-5°C, reaction 1.0-1.5 hours, use acetic acid to neutralize the catalyst, the product contains acetaldehyde 25.19g, enaldehyde 2.73g, β -Hydroxybutyraldehyde is 48.24g, the reaction yield is: 53.60%, and the conversion rate of acetaldehyde is: 72.01%. (2) Preparation of β-hydroxybutyric acid
[0019] Reactant β-hydroxybutyraldehyde 176.8g, solvent ethyl acetate 117.9ml, catalyst cobalt acetate 1.2434, reaction time 3 hours, reaction temperature 60°C, reaction pressure 10MPa, β-hydroxybutyric acid in the product was 43.12g, butene Acid 7.20g, reaction yield: 47.83%, conversion rate: 50.32%. (3) Preparation of ethyl β-hydroxybutyrate
[0020] Reactant β-hydroxybutyric acid 12.19g, ethanol 4.51g, catalyst p-toluenesulfonic acid 1.5g, reaction time is 5 hours, reaction temperature is 80 ℃, β-hydroxybutyric acid eth...
Embodiment 3
[0022] The preparation of embodiment 3 (1) β-hydroxybutyraldehyde
[0023] Reactant acetaldehyde 75g, solvent benzene 60g, catalyst NaOH aqueous solution 22.8g, reaction temperature 7-8°C, in the product, acetaldehyde was 10.45g, enaldehyde was 3.19g, β-hydroxybutyraldehyde was 35.16g, and the reaction yield For: 46.88%, acetaldehyde conversion rate: 86.06%. (2) Preparation of β-hydroxybutyric acid
[0024] Reactant β-hydroxybutyraldehyde 168g, solvent ethyl acetate 150ml, catalyst cobalt acetate 1.1760g, reaction time 1 hour, reaction temperature 50°C, reaction pressure 10MPa, β-hydroxybutyric acid in the product was 26.77g, crotonaldehyde It is 8.16g, the reaction yield is: 28.42%, and the conversion rate is: 33.47%. (3) Preparation of ethyl β-hydroxybutyrate
[0025] Reactant β-hydroxybutyric acid 8.15g, ethanol 1.05g, catalyst p-toluenesulfonic acid 0.73g, reaction time is 1 hour, reaction temperature is 80 ℃, β-hydroxybutyric acid ethyl ester in the product is 5.45g, y...
PUM
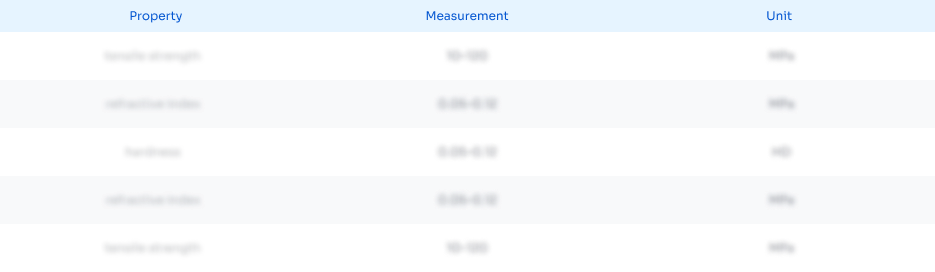
Abstract
Description
Claims
Application Information

- R&D Engineer
- R&D Manager
- IP Professional
- Industry Leading Data Capabilities
- Powerful AI technology
- Patent DNA Extraction
Browse by: Latest US Patents, China's latest patents, Technical Efficacy Thesaurus, Application Domain, Technology Topic, Popular Technical Reports.
© 2024 PatSnap. All rights reserved.Legal|Privacy policy|Modern Slavery Act Transparency Statement|Sitemap|About US| Contact US: help@patsnap.com