Process for making aluminum-plastic ceiling board
A manufacturing process and ceiling technology, applied in covering/lining, construction, building construction, etc., can solve problems such as difficult disassembly and scrubbing, high manufacturing cost, and low strength of aluminum ceilings
- Summary
- Abstract
- Description
- Claims
- Application Information
AI Technical Summary
Problems solved by technology
Method used
Examples
Embodiment approach
[0019] A preferred embodiment of the present invention comprises the following steps:
[0020] (1) Cutting: Cut the aluminum-plastic panels that meet the national standard "Aluminum-plastic composite panels" GB / T 17748-1999 (use 5 pressure rollers to press the panels, and the surface of the feeding panel is covered with blankets to prevent the panels from being scratched. marks), light-controlled automatic control of the cutting size, the diagonal error of the specified size is controlled within ±0.2mm;
[0021] (2) Cutting the four corners: cut the four corners of the plates with the specified size of 330mm×330mm and 630mm×630mm after cutting, and the error of the diagonal after cutting the four corners is ±0.1mm;
[0022] (3) Punching: Punch or press the plate after cutting four corners into a dark bone according to different product processing requirements. The error of hole diameter, spacing and frame is within ±0.1mm;
[0023] (4) Forming (pressing): After punching, the ...
PUM
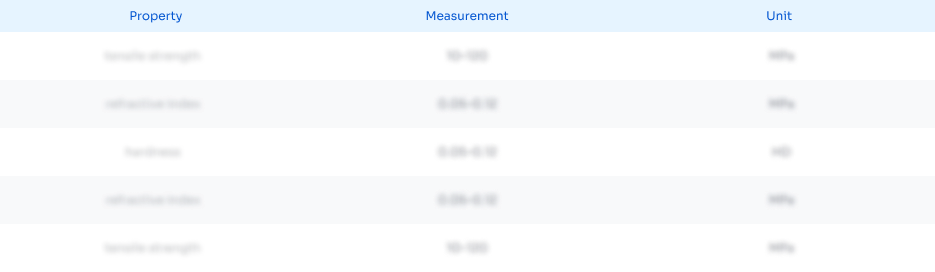
Abstract
Description
Claims
Application Information

- R&D
- Intellectual Property
- Life Sciences
- Materials
- Tech Scout
- Unparalleled Data Quality
- Higher Quality Content
- 60% Fewer Hallucinations
Browse by: Latest US Patents, China's latest patents, Technical Efficacy Thesaurus, Application Domain, Technology Topic, Popular Technical Reports.
© 2025 PatSnap. All rights reserved.Legal|Privacy policy|Modern Slavery Act Transparency Statement|Sitemap|About US| Contact US: help@patsnap.com