Preparation for lipoid frame particle
The technology of skeleton particles and phospholipids is applied in the field of preparation of phospholipid skeleton particles, which can solve the problems of lower cost and price of feed, large equipment investment, large amount of solvent, etc., and achieves simplified oil foot treatment process, less dosage, and is suitable for mass production. Effect
- Summary
- Abstract
- Description
- Claims
- Application Information
AI Technical Summary
Problems solved by technology
Method used
Examples
Embodiment 1
[0013] a. gelatin is first swelled with water and dissolved at 70°C to make a gelatin solution with a concentration of 1 to 5% (weight); sodium alginate is swelled with water and dissolved at 100°C to make a concentration of 1 to 5% (weight). ) of sodium alginate solution.
[0014] b. Use soybean alkalized oil bottoms as raw material, mix evenly according to the ratio of gelatin solution: sodium alginate solution = 1: 0.5 parts by weight, and then make gelatin-sodium alginate mixed solution; press oil bottoms: gelatin-sodium alginate Mixed solution = 1:5 parts by weight, mixed evenly at a temperature of 50°C, transported to the outlet by an auger, made into spherical particles, and filled with CaSO 4 Stay in the saturated solution for 5 minutes, take out the skeleton particles, and dry at 55°C to obtain the product.
Embodiment 2
[0016] a. With embodiment 1.
[0017] b. Use soybean hydration oil foot as raw material, mix evenly according to the ratio of gelatin solution: sodium alginate solution = 1: 2 parts by weight, and then make gelatin-sodium alginate mixed solution; according to oil foot: gelatin-sodium alginate Mixed solution=1:1 weight ratio, mixed evenly at a temperature of 10°C, transported to the outlet by an auger, made into spherical particles, and fed into Na 2 SO 1 Stay in the saturated solution for 10 minutes, take out the skeleton particles, and air-dry at room temperature to obtain a product with good quality and color.
Embodiment 3
[0019] a. With embodiment 1.
[0020] b. Use the peanut hydration oil foot as raw material, mix evenly according to the ratio of gelatin solution: sodium alginate solution = 1: 0.8 parts by weight, and then make gelatin-sodium alginate mixed solution; according to oil foot: gelatin-sodium alginate Mixed solution=1:3 parts by weight, mixed evenly at a temperature of 30°C, conveyed to the outlet by a screw, made into spherical particles, put into 30% ethanol solution for 5 minutes, took out the skeleton particles, and then The product was dried at ℃.
PUM
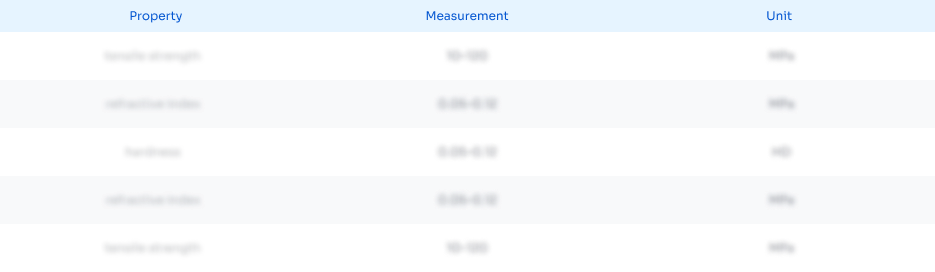
Abstract
Description
Claims
Application Information

- R&D
- Intellectual Property
- Life Sciences
- Materials
- Tech Scout
- Unparalleled Data Quality
- Higher Quality Content
- 60% Fewer Hallucinations
Browse by: Latest US Patents, China's latest patents, Technical Efficacy Thesaurus, Application Domain, Technology Topic, Popular Technical Reports.
© 2025 PatSnap. All rights reserved.Legal|Privacy policy|Modern Slavery Act Transparency Statement|Sitemap|About US| Contact US: help@patsnap.com