Process of preparing polyester slices for high transparent energy saving film
A technology of polyester chips and energy-saving films, which is applied in the field of preparation of polyester chips for energy-saving films. It can solve the problems of high-speed film pulling, poor film adhesion, and low transparency, so as to improve product quality, prevent film breakage, and improve transparency. high effect
- Summary
- Abstract
- Description
- Claims
- Application Information
AI Technical Summary
Problems solved by technology
Method used
Image
Examples
preparation example Construction
[0014] The invention relates to a preparation method of polyethylene terephthalate capable of increasing the film drawing speed. Its process flow is shown in Figure 1:
[0015] Terephthalic acid and ethylene glycol are stirred in the slurry mixing tank according to the set density or molar ratio, the temperature is about 65°C, and pumped into the slurry feeding tank, and the slurry in the slurry feeding tank passes through the pump The slurry injection nozzle enters the esterification tank, and at a temperature of 260-280 ° C, through the circulation of the thermosiphon, the slurry is uniformly mixed and reacted in the esterification tank, and the by-product water and oligomers after the reaction are esterified separated by the separation tower. The oligomers generated after esterification, together with the additives on the pipeline (including cobalt acetate and blue agent or / and red agent) are injected into the pre-polymerization tank through the gear pump according to the ...
Embodiment 1
[0022] Cobalt acetate is injected into the oligomer pipeline behind the esterification tank at a ratio of 0.0025. The blue agent and red agent are injected at a ratio of 0.0025 in the slurry feeding tank. The esterification temperature is 270°C, the precondensation temperature is 285°C, and the absolute pressure 19~20mmHg, the final polymerization temperature is 287℃, and the absolute pressure is ≤1.3mmHg. The proportioning concentration of cobalt acetate is 1.523%; the proportioning concentration of blue / red agent is 145ppm for blue agent and 72ppm for red agent. The molar ratio of blue agent to red agent is 1.5:1. Among them, the contents of cobalt, blue agent and red agent in slices were 9ppm, 0.36ppm and 0.18ppm respectively.
Embodiment 2
[0024] Cobalt acetate is injected into the oligomer pipeline behind the esterification tank at a ratio of 0.0020, and the blue agent is injected into the slurry feeding tank at a ratio of 0.0030. The esterification temperature is 260°C, the precondensation temperature is 290°C, and the absolute pressure is 20mmHg. The polymerization temperature is 285°C, and the absolute pressure is ≤1.3mmHg. The proportioning concentration of cobalt acetate is 1.5%; the proportioning concentration of blue agent is 145ppm. The contents of cobalt and blue agent in slices were 7.2ppm and 0.36ppm respectively.
PUM
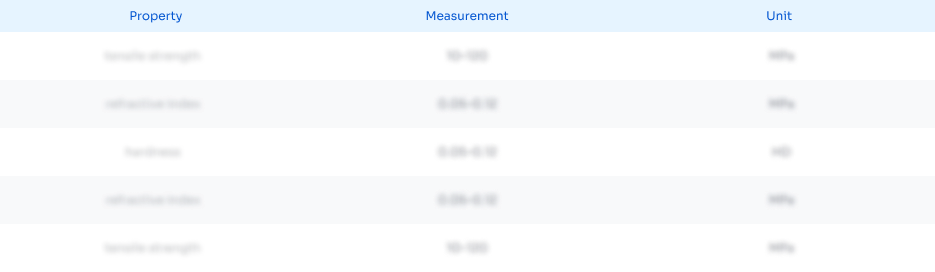
Abstract
Description
Claims
Application Information

- Generate Ideas
- Intellectual Property
- Life Sciences
- Materials
- Tech Scout
- Unparalleled Data Quality
- Higher Quality Content
- 60% Fewer Hallucinations
Browse by: Latest US Patents, China's latest patents, Technical Efficacy Thesaurus, Application Domain, Technology Topic, Popular Technical Reports.
© 2025 PatSnap. All rights reserved.Legal|Privacy policy|Modern Slavery Act Transparency Statement|Sitemap|About US| Contact US: help@patsnap.com