Measuring method for critical electro-discharge machining gap
A measurement method and electrical discharge machining technology, which are applied in metal processing, metal processing equipment, metal processing mechanical parts, etc., can solve the problems of large test error, principle error, and high test cost, and achieve low cost, simple operation, and test. high precision effect
- Summary
- Abstract
- Description
- Claims
- Application Information
AI Technical Summary
Problems solved by technology
Method used
Image
Examples
Embodiment Construction
[0017] The following embodiments are provided in conjunction with the accompanying drawings and the content of the inventive method:
[0018] 1. Preparatory work: Process the side and end faces of the electrode (copper Φ10) on a lathe, and grind the upper and lower sides of the workpiece (material: Cr13, size 50×30) on a grinder, and the parallelism between the upper and lower surfaces is 3 μm. And use sandpaper (600#, 1000#, 1500#, 3000#) to grind the end face of the electrode and the surface of the workpiece until bright. When grinding the electrode, the verticality between the side surface and the end surface is 3 μm,
[0019] 2. Installation: Install the workpiece on the table of the Charmilles 35 series EDM machine tool and tighten it, and then put the electrode into the spindle chuck.
[0020] 3. Setting: Make the electrode and the workpiece at point A (see attached figure 1 ) contact and set the coordinates X=Y=Z=0 of this point A. Then raise the electrode to Z=1mm, ...
PUM
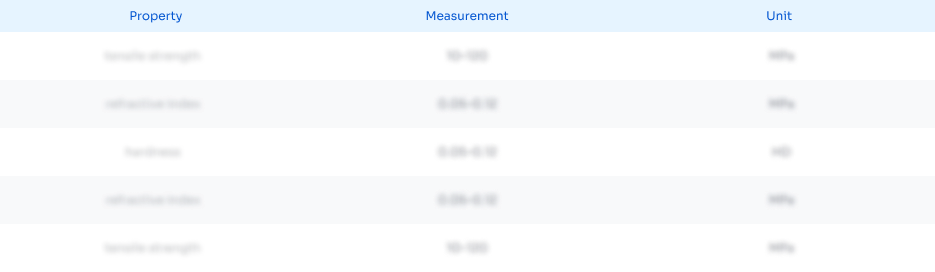
Abstract
Description
Claims
Application Information

- Generate Ideas
- Intellectual Property
- Life Sciences
- Materials
- Tech Scout
- Unparalleled Data Quality
- Higher Quality Content
- 60% Fewer Hallucinations
Browse by: Latest US Patents, China's latest patents, Technical Efficacy Thesaurus, Application Domain, Technology Topic, Popular Technical Reports.
© 2025 PatSnap. All rights reserved.Legal|Privacy policy|Modern Slavery Act Transparency Statement|Sitemap|About US| Contact US: help@patsnap.com