Reaction unit and process of continuous preparation of carbon nano-tube
A carbon nanotube and reaction device technology, which is applied in the field of reaction devices for preparing carbon nanotubes, can solve the problems of high energy consumption, difficult operation of the device, low conversion rate of raw material gas, etc., and achieves low energy consumption and conversion rate of raw material gas. high effect
- Summary
- Abstract
- Description
- Claims
- Application Information
AI Technical Summary
Problems solved by technology
Method used
Image
Examples
Embodiment 1
[0030] Example 1: In the schematic figure 1 Among them, 1 is the catalyst container, which is used to store fresh catalyst, 2 is the catalyst quantitative tank, which controls the amount of catalyst put into the tray each time, 3 is the reaction tower, 4 is the crude product outlet, 5 is the reaction tail gas outlet, and 6 is the raw material Gas inlet, 7 is a valve, 8 is a tray, 9 is a connecting mechanism, through which the tray is connected with mechanical equipment to control the movement of the tray, 10 is a scraper, responsible for transferring the material on the tray to the next tray, 11 is the upper gate of the catalyst quantitative tank, 12 is the lower gate of the catalyst quantitative tank, 13 represents the first tray, 14 represents the second tray, 15 represents the third tray, 16 represents the fourth tray, 20 is the first group of trays, and 21 is the second group of trays.
[0031] Combine below figure 1 Explain the process of continuously preparing carbon n...
Embodiment 2
[0035] Embodiment 2: The continuous preparation of multi-walled carbon nanotubes of different specifications can also be realized by using a tower reactor. Such as figure 2 As shown, the upper tower reactor 30 is placed on the lower reaction tower 31 to form a combined reaction tower, so that the activation of the catalyst and the growth of carbon nanotubes can be carried out at different positions simultaneously, and multi-walled carbon nanotubes of different specifications can be realized. Continuous production of tubes. Among the combined tower reactors, the upper tower reactor 30 is used to activate the catalyst, and the lower tower reactor 31 is used to prepare carbon nanotubes. The two tower reactors are connected through a catalyst container 1 and a catalyst quantitative tank 2 . After the catalyst is activated by the upper tower reactor 3 (), it falls into the catalyst container 1 of the lower tower reactor 31, is quantified by the catalyst quantitative tank 2, and ...
PUM
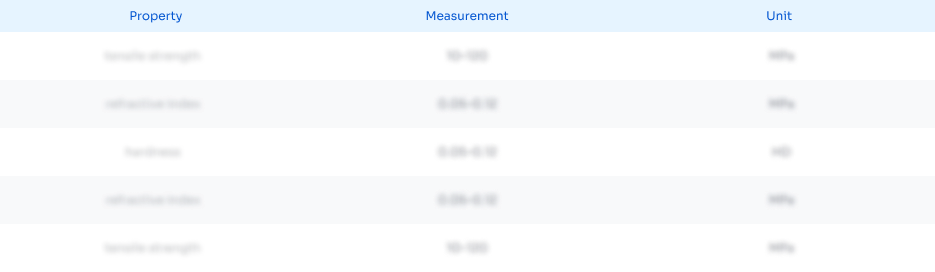
Abstract
Description
Claims
Application Information

- R&D Engineer
- R&D Manager
- IP Professional
- Industry Leading Data Capabilities
- Powerful AI technology
- Patent DNA Extraction
Browse by: Latest US Patents, China's latest patents, Technical Efficacy Thesaurus, Application Domain, Technology Topic, Popular Technical Reports.
© 2024 PatSnap. All rights reserved.Legal|Privacy policy|Modern Slavery Act Transparency Statement|Sitemap|About US| Contact US: help@patsnap.com