Locomotive gear wheel box and its production method
A technology for gearboxes and locomotives, which is applied to transmissions driven by electric motors, transmissions with rotating prime movers, etc., can solve problems such as oil leakage and easy cracking, and achieve high interchangeability, reduced box weight, The effect of reduced strength requirements
- Summary
- Abstract
- Description
- Claims
- Application Information
AI Technical Summary
Problems solved by technology
Method used
Image
Examples
Embodiment Construction
[0022] The manufacture method of locomotive gear box of the present invention comprises following processing steps:
[0023] The 2-5mm steel plate that has been blanked, preferably 2-3mm steel plate, is cold-stretched or hot-stretched multiple times to form the box profile of the upper cover 1 and the lower cover 2; Reinforcing ribs 6, reinforcing ribs 7, and hanging welding bosses 8 are formed on the surface of the box body; and then through multiple cold pressing and punching to form oil standard seat welding bosses 9; and then through multiple punching, flanging, and pressing , forming the upper cover interface flange 11, the lower cover interface flange 12 and the seam 4 for installing the sealing strip 5, the seam 4 can also be formed by welding after being made separately; then the upper cover 1, the lower cover 2 and the The reinforcing support rib 13 formed by cold pressing for many times and the coupling nut welding boss 10 formed by cold pressing for many times, the ...
PUM
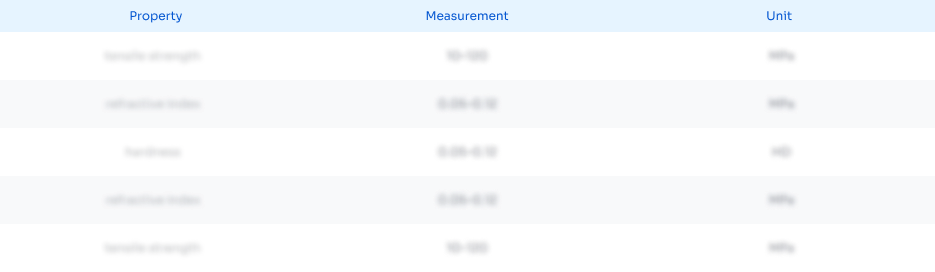
Abstract
Description
Claims
Application Information

- R&D Engineer
- R&D Manager
- IP Professional
- Industry Leading Data Capabilities
- Powerful AI technology
- Patent DNA Extraction
Browse by: Latest US Patents, China's latest patents, Technical Efficacy Thesaurus, Application Domain, Technology Topic, Popular Technical Reports.
© 2024 PatSnap. All rights reserved.Legal|Privacy policy|Modern Slavery Act Transparency Statement|Sitemap|About US| Contact US: help@patsnap.com