Aircraft air tightness test equipment and air tightness test method
A test equipment and air-tightness technology, which is applied in the direction of aircraft component testing, liquid-tightness measurement using liquid/vacuum degree, and measurement of fluid growth and deceleration rates, etc., can solve low reliability, potential safety hazards, and inconvenient transportation and other issues to achieve the effect of improving reliability and accuracy, facilitating portability and transportation, and avoiding operational errors
- Summary
- Abstract
- Description
- Claims
- Application Information
AI Technical Summary
Problems solved by technology
Method used
Image
Examples
Embodiment Construction
[0038] The present invention will be further described in detail below with reference to the accompanying drawings and specific embodiments.
[0039] As shown in this disclosure and the claims, unless the context clearly dictates otherwise, the words "a," "an," "an," and / or "the" are not intended to be specific in the singular and may include the plural. As used in this disclosure, "first," "second," and similar words do not denote any order, quantity, or importance, but are merely used to distinguish the various components. Likewise, words like "comprising" or "comprising" mean that the elements or things appearing before the word encompass the elements or things recited after the word and their equivalents, but do not exclude other elements or things. Words like "connected" or "connected" are not limited to physical or mechanical connections, but may include electrical connections, whether direct or indirect.
[0040] Figure 1 to Figure 3 An embodiment of an aircraft airt...
PUM
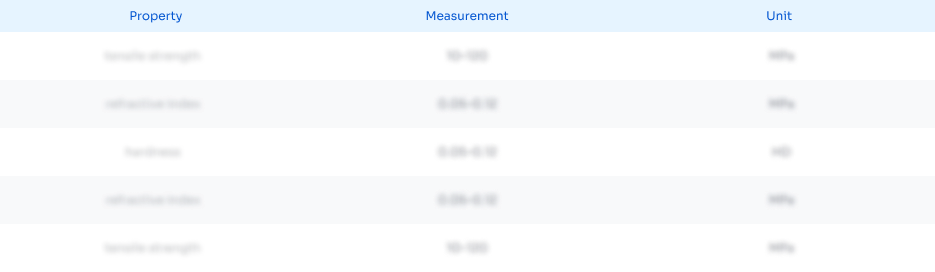
Abstract
Description
Claims
Application Information

- R&D Engineer
- R&D Manager
- IP Professional
- Industry Leading Data Capabilities
- Powerful AI technology
- Patent DNA Extraction
Browse by: Latest US Patents, China's latest patents, Technical Efficacy Thesaurus, Application Domain, Technology Topic, Popular Technical Reports.
© 2024 PatSnap. All rights reserved.Legal|Privacy policy|Modern Slavery Act Transparency Statement|Sitemap|About US| Contact US: help@patsnap.com